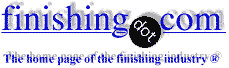
-----
Abrasive Resistant, FDA approved Aluminum Coating Needed

I am looking for an FDA approved coating, for aluminum parts that are used in the pharmeceutical process of making pills. The coating currently used is a teflon impregnated hard coat, which is failing due to the abrasive properties of the granulation involved. Is there a better coating to use or will I have to consider manufacturing the parts out of a different material?
Ken Schumacher- Palatine, Illinois
2003
A. Whether any aluminum coatings are actually 'FDA approved' has been a topic of discussion here many times. So far the answer seems to be that no coatings are actually 'approved'; rather, they are not prohibited if they are "Generally recognized as safe". But that discussion continues.
Anodized coatings are quite abrasion resistant. Is it possible to use a hard coat without teflon? If not, then it would seem that a PVD processes to apply TiN, or a similar process to apply diamond-like-carbon, flame spraying, or electroplating a composite that includes diamond particles are among the few coatings that are harder than hard anodizing.
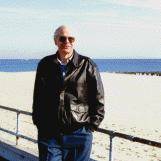
Ted Mooney, P.E.
Striving to live Aloha
finishing.com - Pine Beach, New Jersey
A. Hardcoat anodize is hard but has poor lubricity or sliding wear. Hardness is measured by stabbing a part. Hardness does not have much to do to do with sliding or abrasive wear.You are looking for a coating that has good sliding wear or lubricity. High phosphorous electroless nickel is approved for that application.Electroless nickel frequently works when anodize fails as it has has much better lubricity than hardcoat anodize.The high phos EN is about 45RC as plated . It can be hardened to 65 RC at 400c. Electroless nickel can easily be stripped from aluminum without damaging or shrinking the part. This allows parts to be repeatedly stripped and replated as they wear out.
Todd Osmolski- Charlotte, North Carolina, USA
Q. I also work in a tableting industry where an abrasive product wears on machine parts. I have been asking about a possible solution using a hard coat . We currently use an anodized and nickel coating. I was wondering about porcelain coating. Friction does pose a problem for us with some products.
Dennis Guenther- St. Louis, Missouri, USA
2007
A. I must chime in here, and say that the lubricity of HardCoat anodizing can be increased with the impregnation of PTFE into the coating.
I have not performed the required suga, Taber testing to back up my statement here, but I do know that the hardness of HC anodizing outperforms EN and with the PTFE I am sure that the lubricity would be competitive.
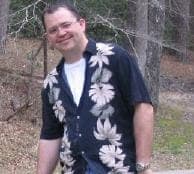
Ryan Cook
Toccoa, Georgia
Q, A, or Comment on THIS thread -or- Start a NEW Thread