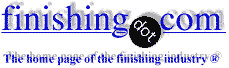
-----
Bead blasting aluminum before clear anodizing. Cosmetic problem.
November 30, 2020
Q. Hi,
I'm having some issues creating a consistent finish on beadblasted aluminium.
in terms of process here some things we are trying:
• blasting in a consistent pattern/distance away from the part.(visual inspecting shows even coverage)
• Ultrasonically cleaning the part for 3seconds to remove particulates
• Etch in NaOH for 1:30min
• Gloved process to protect from contamination
• Part isn't allowed to dry out throughout the process.
• Everything is made with deionised water
• ti racked
• agitation
Picture below shows the part as anodised 0.4A (initial voltage 4v rising to 8 v) for 10 mins @ 20 °C before going into a cold seal for 10mins @ 30 °C
Thanks for your help
Phil
- London UK
A. The defect is due to bead blasting not good enough (uneven, in order to blast the small hole ID, areas close to the hole will end with thick blasting if the rest area not properly being compensated). Actually you could find out the uneven defect right after etching and desmut but before your anodizing.
John hu
- Singapore
December 3, 2020
⇩ Related postings, oldest first ⇩
Q. Dear Sir,
We are having problems with clear anodized aluminum parts. We are trying to maintain cosmetic uniformity across a variety knobs with a circular grain satin finish on the face and knurled on the outer diameter. Our supplier states that he takes great care in diamond turning the parts only to have the anodize vendor return them with varying light and dark areas that follow the circular tool marks (like a bullseye effect). Over the past four years he's had a maximum of six consecutive months of uniform parts. The rest of the time he's sorting approximately 30% for poor cosmetic quality. He has changed material suppliers to try to eliminate contaminated material variation. Is the problem material related or cleaning & anodize process related?
James K Kessel- Depew, New York
1998
A. Sir,
I run 2 large, job shop anodize plants.
The problem could be with the anodize or anodizer as we have never really had such problems. We do lots of cosmetic work.
David A. Kraft- Long Island City, New York
1998
A. It sounds like a racking problem to me. Dark areas on clear anodized parts could be a result of parts losing contact and alloying elements plating back onto the parts, particularly if the knobs are a high copper alloy. Either the anodizer doesn't have a good rack for holding these knobs, or they are working loose somewhere in processing. The "bullseye effect" could even be from arcing due to intermittent contact of loose parts on the rack. Maybe the anodizer is trying to bulk anodize the parts, where a certain percentage of non-anodized parts would be encountered.
If the problem is indeed with the anodizer, as it appears, I must say that no GOOD anodizer would let finished parts go out the door with 30% rejects, particularly when the cause for rejects is highly visual. In these days of quality-oriented production, any good anodizer needs to have an edge over his competitors, and usually the only way of showing customers how good his shop is, is to deliver a quality finish on any parts that he processes. I believe your supplier needs to find another anodizer or demand a major shake-up of the present anodizer's quality methods.
Phil Johnson
- Madison Heights, Michigan
1998
A. I think you may have problems with the smoothness of the part. It may be the anodizing is highlighting the imperfection of the part. I have run anodizing lines for 30 years. I have seen problems like this before.
adv.
If you would like to send me some of the parts to view, I might be able to help you.
1999
I must commend the response directed towards any "GOOD Anodizer" would never ship parts with a 30% reject trend. I have noticed that with today's market of quick turn orders meshed with cost of operating reductions that some outside process vendors are having troubles balancing operations and cut too many corners when cutting costs. One of the biggest mistakes American Industry might make would be to fall short on their "BQS", Basic Quality Standards. Shipping parts to your customer with a 30%...20%...10% failure rate is never ok. Businesses that continuously accept deliveries like this are just as guilty as the vendor shipping the parts in such unacceptable conditions. If American Industry wants to be leaders in manufacturing we need to quit finger pointing, quit accepting lame excuses and most of all address issues with intent to resolve them.
I 100% agree that the Anodizer shipping 30% rejects shouldn't have the opportunity to be so irresponsible and degrade your products.
Leslie J. Cantu- Milpitas, California, USA
2001
Multiple threads merged: please forgive chronology errors and repetition 🙂
Q. I have a customer who bead blasted the aluminum parts (small, 1125 pieces/rack)and wanted us to black anodize. I told him that the black dye could be shaded due to the unevenness of the bead blasting. We etched/anodized and dyed black and the parts are a dark gray to black on the same surface. We are willing to re-anodize...do we extend the etching process to get a "mat" finish. Any other suggestions? Should we etch for a longer period when parts are bead blasted? We use caustic to etch.
Gus Nordgren- West Palm Beach, Florida
2002
A. Gus,
One way to even the blasted surface is to perform a two step process. Run parts through your normal caustic etch before anodizing. Anodize parts until you have reached an approx. thickness of .0003 then strip parts again in the caustic bath. If you can follow up with a Nitric/HF bath after the caustic strip is even better. After stripping the parts re-anodize & dye. This process will smooth out the high and lows of poor and uneven blasting.
David Hendrick- Round Rock, Texas
2003
A. Be sure that the beads are designated aluminum only. If they use the same beads on iron, copper, or magnesium, or any other metal, then you pound giblets of foreign metal into the aluminum which will lighten the shade of the black dye. Again, as the man said above, etch the hell out of it to remove the beaded-in non-aluminum.
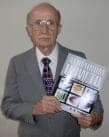
Robert H Probert
Robert H Probert Technical Services

Garner, North Carolina
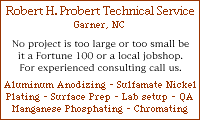
2003
Multiple threads merged: please forgive chronology errors and repetition 🙂
Blotchy clear anodized finish on bead-blasted 5052 AL
June 3, 2009Q. Hello.
We are making a part for a customer that requires a Class A (perfect!) clear cosmetic anodized finish. It is folded out of .125 5052 H-32 AL. The folds are tight enough that there is some fracturing on the outside of the folds, so we are DA sanding before fold, DA sanding after fold (to minimize fractures and folding marks), and then bead-blasting as the final prep before anodizing.
The problem is that we are getting inconsistent results from the clear anodizing process that we sub out. There are blotchy areas that are easily noticeable, and unacceptable, for this class A, cosmetic part. We are also doing a couple other parts out of thinner material (similar processes, but less DA needed)and those don't seem to be having the same problems.
I have found a few similar letters in this forum, but none addressed 5052 AL so I figured I would ask a more pointed question. What I have found as possible causes in other letters:
Inconsistent bead-blasting, bead-blasting with dirty media or incorrect media, bead-blasting is being done with the wrong technique (wrong angle, pressure?),etch at the anodizer is not the correct process
I will also note that the bead-blast finish is not specified by the customer. They just require a fine, even, consistent finish after clear anodizing. We do need to sand the fractures, so that is unavoidable, but maybe bead-blasting is not the best choice?
Any advice will be greatly appreciated.
TIA
Erik
Fabricating Shop Purchasing Agent - Boise, Idaho, USA
A. Two problems.
(1) The manual held bead blasting wand is not leaving a uniform finish. It looks great to the naked eye, but the anodizing magnifies the varying splotches.
(2) If the media has been used on any other metal (iron, brass, etc) then you are imbedding that metal into the soft (Kleenex-like) aluminum. Imbedded iron in an aluminum anodizing tank is oxidized to reddish color.
(3) There is a possible third problem in that where the bend is located the surface is different from the other flat surfaces and this skews the (otherwise) vertical pore structure.
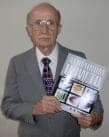
Robert H Probert
Robert H Probert Technical Services

Garner, North Carolina
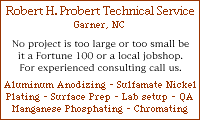
June 8, 2009
Treatment &
Finishing of
Aluminium and
Its Alloys"
by Wernick, Pinner
& Sheasby
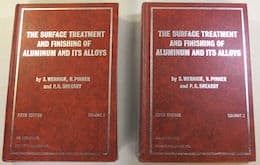
on eBay or Amazon
or AbeBooks
(affil link)
Q. Hi sir,
I have a project on a deep drawn sheet metal aluminium part. It's having anodization process after finishing, but due to uneven surface finish by buffing, it causes several visual defects on it. So I tried glass blasting before anodization. But after the anodizing process the parts are totally colour changed. I cannot give an even surface finish to inner and outer sides of the part. So please advise me.
aerospace - Chennai,Tamil nadu, India
June 6, 2015
A. Dear Sir,
Buffing and blasting are 2 different processes with different purpose. Buffing is generally used for gloss finish and also for removal of deep scratches.
While blasting with glass beads is used for satin matte finish and also for removal of extrusion lines. Just make sure what bead size you are using; generally 80 or 60 is been used. Make sure the blasting is at even psi. Anodizing is good on 6063 alloys. Also check the alloy which you are using.
Happy Anodizing
- Ahmednagar Maharashtra India
July 11, 2015
A. To get a matte black finish on 6061 T6 aluminum, bead blast with 110-170 glass bead at around 60 psi. We've done 1000's of parts this way.
Denie Leslie- Hollister, California
July 26, 2016
Multiple threads merged: please forgive chronology errors and repetition 🙂
Q. We manufacture firearm parts for military/civilian use. We outsource anodizing to a local company. We are having an issue with a cosmetic flaw that appears on only one area of the part.
The flaw looks like a lightening bolt or mountain range profile, has no apparent depth even under microscope, and looks medium to dark gray as opposed to the black finish. The flaw size is about 1/4 to 1/2 inch tall and 1/2 to 1 inch long with 4 to 20 peaks or zigzags.
Parts are 7075T6 forgings, tumbled, ceramic bead blasted, and racked on aluminum racking. The flaw is very close to the rack contact (hole) but does not begin or end at the hole. Racking has been tried thru the hole from both directions and the flaw still appears only on one side of the part, never on the opposite side or anywhere else.
We have anodized about 5000 parts in the past few weeks and have a fallout from this issue in approx. 500 parts. Some parts have been stripped, re-blasted, and re-anodized. The last group of redo's was 350/7 parts/fallout for the same condition. Any ideas on where to look to remedy this issue?
buyer - Muncie, Indiana USA
September 21, 2009
A. Let's look (1) for imbedded iron from the tumble media and (2) for work hardening in the particular area which may have migrated the zinc into grain boundaries near the surface where the anodizing layer cut all the way thru to the zinc rich spot and fell out. Then let's look at the agitation pattern and see if air is hitting that spot and displacing sulfuric acid.
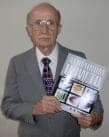
Robert H Probert
Robert H Probert Technical Services

Garner, North Carolina
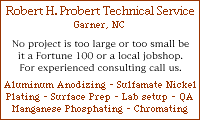
September 23, 2009
![]() |
Q. Thank you for the response. Our tumble media is ceramic and is dedicated to 7075 aluminum only. Our blast media is also ceramic and is also dedicated. We are using three suppliers of forgings and we seem to have the same problem with all three sources. I will check on the fixturing of the parts to determine if work hardening could be caused by the clamping. I forwarded images of the issues to this site.
- Muncie, Indiana USA September 24, 2009 A. Brian - Colorado Springs Colorado September 24, 2009 |
Q. I tried David Hendrick's two step method on sheet metal samples, and after re-anodizing the parts looked much more uniform but wouldn't take any dye. Then after drying showed some strange slightly darker areas like sprinkles of dirt.
Ted Mitchell- Jay, Oklahoma, USA
September 4, 2016
Major Problems with cosmetic part anodizing!
Q. Hello!
We are having major problems with a cosmetic part we are trying to manufacture, I am hoping that the experience on this site will help! We machine the parts in our shop then send them away to be media blasted. Our blaster says that they use a "proprietary" blend of sand and glass...
We then took them to be clear anodized and found that the surface finish was blotchy and generally terrible! I would be happy to post photos. Do you have any suggestions for how we can recover these parts?
- Calgary, Alberta, Canada
March 22, 2017
----
Ed. note: E-mail the pics to
A. Pictures of the parts as blasted, and after anodizing would be very helpful.
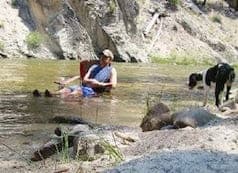
Marc Green
anodizer - Boise, Idaho
March 23, 2017
A. If the surface contamination isn't too excessive, then a good long strip-etch and anodizing again will fix the parts, run few of them as a test before doing the whole batch.
What usually happens is that blasting person will turn the pressure up near max available to speed things up - and this breaks up media and embeds the dust into the surface of the soft aluminum part - and normal etching/desmut times simply may not be enough to remove that dirty layer - even more problems may arise if they used that same blasting media to clean a rusty steel part before - and none of them will not admit any of this - but that is what ruins the parts.
My personal opinion - blasting is the last possible option to prep aluminum part for anodizing, and even then it has to be done properly and complicates desmutting process a little, I usually turn these orders away and send them to paint shops - because the result is simply too unpredictable.
private - Riga, Latvia
March 24, 2017
Q, A, or Comment on THIS thread -or- Start a NEW Thread