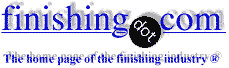
-----
ASTM B-633 Type II vs. III zinc plating

Q. We are getting poor coverage on the as-cast surface of some steel castings using a yellow Zinc chromate. Our plater would like to go to a clear zinc, but our customer is under the assumption that the clear will not do as good a job with corrosion resistance and salt spray life. He is asking for more info on the difference between ASTM B633 type II and type III. Can anyone give me some direction on how to get the customer to accept going to clear. Our plater said that he would be willing to go thicker on the clear. Also, I found out that the casting is painted after plating. Does plating make that big a difference knowing that it's going to be painted also?
Mark Hollenbeckalloys - Muskegon, Michigan
2002
![]() |
A. Surfaces left-bare should be heavily chromated. Surfaces to be painted should be ONLY lightly chromated. A heavy chromate will shear under paint and cause the paint to peel. Put the chromate on light. A light yellow would be better than a clear. This applies to all metals. In the case of castings you may get some out-gassing and/or bleeding from the porosity. ![]() Robert H Probert Robert H Probert Technical Services ![]() Garner, North Carolina ![]() A. Type III refers to a clear (blue brite) chromate (passivate); Type II refers to a colored (yellow, olive drab)chromate. I believe it is ASTM B201-80 that states you should get at least 24 hrs to white corrosion from a single dip clear (blue brite) chromate in a salt spray cabinet. Yellow chromate should get 96 hrs to failure. Olive Drab chromate is 150 hrs. The end user must decide when a part fails, at "white rust" corrosion (the chromate has failed) or red rust (both the chromate and the zinc are gone exposing the base metal). Don Penzenik- Elkhart, Indiana |
A. The problem may not be with the chromate at all. Going with clear will make it difficult to tell what is clear chromated zinc vs. what is bare steel (except for the rust that is likely to appear). What type of zinc plating bath is your plater using? Certain castings are difficult, if not impossible, to plate in either cyanide or alkaline non-cyanide plating baths. Try using an acid zinc chloride bath and see if the casting covers.
I will be attending the ASTM B8 committee meetings in Philly later this week (2002) and will mention this letter to the sub-committee chair responsible for the B-633 spec.

Milt Stevenson, Jr.
Syracuse, New York
2002
----
Ed. note: The above entries are somewhat dated: because of RoHS regulations, most platers have switched from hexavalent to modern trivalent chromating, and the corrosion resistance of the coating is no longer related to its color; in many cases the yellow color nowadays is simply dye.
Multiple threads merged: please forgive chronology errors and repetition 🙂
Q. I cannot get a straight answer -- Zinc plating, zinc plating with chromate, Type II, III, etc. All I need to know is what color the types are. Here we use clear & yellow zinc plating ... also use the terms bleached and unbleached -- which I haven't heard of until I got here. Any information would be well received.
Ron Werkheiser- Stroudsburg, Pennsylvania
2002
A. It's pretty simple, ASTM B633 Type II coatings indicate a colored chromate; gold, black etc.; Type III coatings are colorless or clear chromate (iridescent okay). The Standard default is gold for type II coatings unless otherwise specified.
Bill Grayson- Santa Cruz, California, USA
A. And yes, some shops bleach/leach the strong gold/yellow color back to a very faint color by immersion in a hot rinse tank -- although some believe that if the color is gone, the protection is gone. I've seen this done less commonly on chromated zinc plating than on chromated aluminum.
Regards,
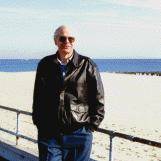
Ted Mooney, P.E.
Striving to live Aloha
finishing.com - Pine Beach, New Jersey
Multiple threads merged: please forgive chronology errors and repetition 🙂
ASTM B633 and Hexavalent Chromium
Q. I need to specify platings that do not contain Hexavalent Chromium for parts that will be used in the automotive industry. Do I need to specifically call out the use of Trivalent Chromium, or is it covered in the specifications used for ASTM B633?
1 Do all ASTM B633 Type II platings use Hexavalent Chromium?
2 Can you get a type II finish that uses Trivalent?
3 Do all ASTM B633 Type III platings NOT use Hexavalent Chromium?
4 I have not heard much about the Type IV finishes. Do they use Hex or Trivalent chromium, are they available in colours, and do they protect as well as the type II or III finishes?
If anyone knows of a good plating guide to pick up, please let me know.
Claudio ZubinAuto Parts - Winnipeg, MB, Canada
2005
Q. I have the exact same questions. Did you ever get the answers you were looking for? Does anybody know this info?
Doug Kovacs- North Canton, Ohio
2005
A. Hello Claudio and Doug,
My compliments for an excellent round of questions!
In response to your questions re ASTM B633; I have an old version of the spec so my opinions are based upon the one I have.
1 Do all ASTM B633 Type II platings use Hexavalent Chromium?
Ans: The answer is Yes. ASTM B633 and all other worldwide standards were written around the time when no one spoke about trivalent. It definitely implies Hex Chrome.
2 Can you get a type II finish that uses Trivalent?
Ans: Trivalent chromates give paler and lighter finishes; some use metals, some use permanganates, some use dyes, in order to replicate the Hex finish. You can get the same finish only for blue and black hex chrome with tri substitutes, but not for yellow or olive as of yet. A Blue with pale yellow is the best replacement for yellow as of now.
3 Do all ASTM B633 Type III platings NOT use Hexavalent Chromium?
Ans: No it does not imply that. Type III (colorless) generally refers to Hex Chrome that has been bleached off to give a clear look. It still will have Hex Chrome.
4 I have not heard much about the Type IV finishes. Do they use Hex or Trivalent chromium, are they available in colours, and do they protect as well as the type II or III finishes?
Ans: In 24 years I have only been asked this question once before and I presume it involves phosphating over zinc plating for those heavy phosphating grammage applications, where normal phosphating will not provide enough zinc phosphate that is required in the deposit. No, other colors may not be available if my presumption is right.
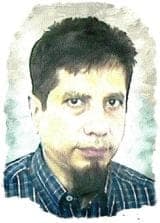
Khozem Vahaanwala
Saify Ind

Bengaluru, Karnataka, India
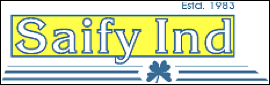
A. As far as I remember the RoHS Directive asks for no more than 1000 ppm (0.01%) of hex Cr of an homogeneous item.
To calculate it is very difficult, as the plating is a few molecules thick. According to RoHS the homogeneous and non-homogeneous are defined in such manner that every one may understand that the layer is removable (let's see how).
In my opinion a MIL-C-5541 plating withstands the 1000 ppm that means that the plating passes the barrier (at least on aluminium plates).
What do you say?
- Oranit, Israel
Q. Our Customer has specified on the print, "Zinc chromate per ASTM B633, Fe/Zn Type II Clear." We are not sure what is meant by, "Fe/Zn Type II".
Could you explain this?
Thanks,
Product Engineer - Cincinnati, Ohio
2007
A. I'm not a zinc plater, but 'Type II Clear' seems self-contradictory.
See ASTM B633-07, 'Standard Specification for Electrodeposited Coatings of Zinc on Iron and Steel.'
Fe/Zn Type II indicates an iron or steel substrate, electroplated with zinc, followed by a Type II treatment (colored chromating).* Two problems with the given print specification:
1) Zinc thickness isn't given, and
2) 'Clear' isn't defined in B633 but ASTM B201-80 mentions 'colorless (clear bright).' Colorless chromate is Type III per B633.
Perhaps some confusion with Service Condition (SC) 2 (moderate), which indicates a minimum zinc thickness of 8 microns and is commonly clear chromated (Type III). In this case, the designation would be Fe/Zn 8 Type III.
Type II chromates are more commonly used where greater corrosion resistance is required, e.g., for SC3 & SC4 (13 & 25 microns zinc, respectively). Obviously, this must be clarified by the customer. Also, some yellow chromates are clear w.r.t. opacity, although this is not platers' usage.
*Note: Answer is based upon pre-2007 versions of B633 (1985, 1994, 1998). The 2007 revision addresses RoHS concerns and specifically allows non-hexavalent chromate treatments.
- Goleta, California

Rest in peace, Ken. Thank you for your hard work which the finishing world, and we at finishing.com, continue to benefit from.
Q. We have a callout for "Bright Blue Zinc Plating", type II, SC3 per ASTM B633. The part is currently being produced in China and my local platers are suggesting a dye to get a blue color. That seems a bit discretional to me. Is this process done in the United States, and if so by whom?
Rich Farnham- Huntersville, North Carolina
April 24, 2009
A. Hi, Rich. To me "bright blue" does not usually literally mean "bright blue" like the sky or a robin's egg. It would be "bright, blue" -- that is, shiny and metallic but with a bluish rather than a yellowish cast.
But if you are looking for something indisputably blue, as opposed to clear with a possible slightly bluish cast, this probably requires dye. As the USA moved toward metric fasteners, for a while there was a move to dye them blue. The color was known as "metric blue", which apparently is also a company name/trademark (although I don't know whether the chicken or the egg came first).
Until a very few years ago chromate conversion coatings were based on hexavalent chromium, and deposited a thick film that was relatively easy to dye. Some of today's proprietary trivalent chromium coatings are very thin and consequently will not generate a highly saturated color though.
Zinc plating is usually considered a functional coating, not a decorative one. So if you need to color match, you need to do it with a requirement for compliance with sample parts -- not a verbal description. Good luck.
Regards,
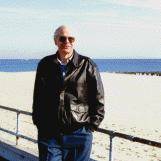
Ted Mooney, P.E.
Striving to live Aloha
finishing.com - Pine Beach, New Jersey
Zinc Chromate Per ASTM B633 Type II
Q. Does the Type II in spec ASTM B633 designate the color Zinc Yellow. How do you know if it is supposed to be Zinc Yellow or Zinc Clear?
Chris BertuzziQA Technician - Pinebrook, New Jersey
May 20, 2009
Difference Between ASTM B633 TYPE III & Type II
Q. Difference Between ASTM B633 TYPE III & Type II? I am not getting the difference between this. Is there any colour difference OR is there any Salt spray difference?
kaushik HVNew Product Development - Bangalore,Karnataka, India
August 28, 2015
A. Kaushik,
The "Types" define supplementary finishes to be done after the plating.
II says "colored chromate coatings" meeting 96 hours of salt spray, and III says "colorless chromate conversion coatings" meeting 12 hours of salt spray.
Both should be finished according to ASTM B201-80 and tested according to ASTM B117.
So if I'm interpreting this correct, there is both a color difference and a salt spray difference. III is colorless and not expected to hold up as long as the colored II.
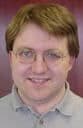
Ray Kremer
Stellar Solutions, Inc.

McHenry, Illinois
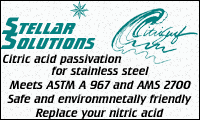
Two Different Colors of Zinc Plate Clear Chromate ASTM B633, SC2 Type 5
Q. Hi,
I recently received 2 batches of parts from two separate platers using this specification.
Zinc Plate Clear Chromate ASTM B633-15, SC2 Type 5
However, I noticed that one batch of parts from supplier A had a blueish tint, while the second batch of parts from supplier B had a whitish tint. What process variation would produce these different results?
Thanks
- Long Beach, California USA
December 27, 2018
A. Hi Kyle. Different brands of chromate conversion chemistry, possibly different plating processes (acid zinc vs. alkali zinc). This is not considered a decorative finish and will not generate matching parts. Sorry, but if you need one particular look, you must go through the ugly process of maintaining sample boards with acceptable vs. unacceptable finishes. Good luck.
Regards,
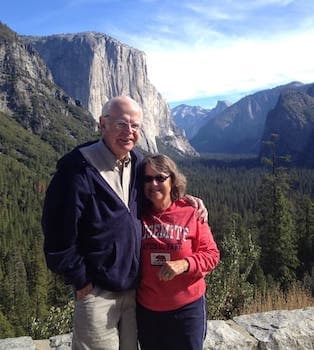
Ted Mooney, P.E. RET
Striving to live Aloha
finishing.com - Pine Beach, New Jersey
A. We always noted the coating for our application as 'Zinc Plate: Type II, CL 3, Clear w/Blue Tint.
G Manning- California
July 4, 2022
Q, A, or Comment on THIS thread -or- Start a NEW Thread