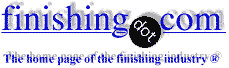
-----
Zinc Phosphating: Improving the Formula

9th Edition, Vol. 5
"Surface Cleaning, Finishing & Coating"
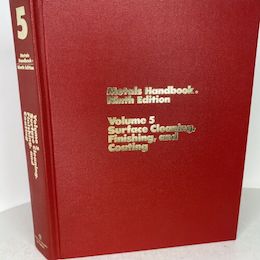
on eBay or Amazon
or AbeBooks
(affil link)
Q. I am looking for a high quality zinc phosphate solution that has uniform coverage and good corrosion resistance and is also suitable for painting.
When I want to dissolve zinc oxide in phosphoric acid, if the amount of zinc oxide exceeds a certain limit, it is not dissolved in phosphoric acid and zinc oxide particles are scattered and precipitated in the form of white grains in the solution, and this makes the solution I don't have proper phosphate.
Ingredients I use for zinc phosphate in 100 ml volume:
Zinc Oxide 1/8 g
Phosphoric acid 4/5 g
Sodium nitrate 0/5 g
Any information on this topic will be greatly appreciated.
- Mashhad, Iran
July 2, 2024
⇩ Related postings, oldest first ⇩
Q. To whom it may concern, hello,
We would like to introduce ourselves as a chemical company. We are in the process of zinc phosphating with Nitric acid, phosphoric acid and zinc oxide and the major problem we face is due to the low salt spray resistance. We think the non-uniform coating causes this problem. How we can increase the time of salt spray resistance?
Best regards,
- Tehran, Iran
2002
A. Dear inquirer,
Your problem may be because of improper ratio of basic three chemicals and it may further require some special additive like nickel, etc.
Thanks,
- New Delhi, India
A. Hi,
Give a few more details. Are you processing by dip and is this prepaint or an oiled finish you are referring to? The formulation is far too simple for high performance.
- Croydon, U.K.
Q. Dear Mr Maheshwari and Mr Bridger,
Thank you for answering. Our formulation consists of : Phosphoric acid : 48% Nitric acid : 11% Nickel Carbonate : 1.01 copper carbonate
⇦ on
eBay
or
Amazon [affil links]
: 0.01 Zinc Oxide : 14.70 and the accelerator is NaNO2. It is processed by dip and for prepaint. With above formulation with 16 g/L Zinc Phosphate the results were: Free acid : 2 Total acid : 12 We need to decrease the amount of free acid for less than 1 point , but whenever the amount of FA comes down (less than 1 ) precipitation occur in concentrated phosphate. So how can we decrease the amount of free acid without precipitation and having a good salt spray after phosphating? Our actual salt spray with above formulation is: 23 hours.
Thanks,
- Tehran, Iran
A. Dear Mr Sara Abiri,
From your reply I must assume you are sealing the phosphate with an oil. If you not using any seal at all then salt spray resistance will be minimal. The ratio of free acid to total acid will be temperature dependent. The higher the bath temperature the higher the ratio. Thus at 50 deg or less a 10:1 ratio is possible but on heating to 70+ the ratio will drop to 6:1.
If you want a heavier coating you could try operating on the iron-side (no accelerator. Temp will need to be above 75 °C. If you require a finer crystalline coating you will require a Ti activated predip or 2 g/l oxalic acid predip.
- Croydon, U.K.
Q. Dear Mr Bridger,
Thanks for your information. Would you please let us know your opinion about the mole ratio of Nitric acid to Phosphoric acid ? Any advice that could be given would be much appreciated.
Best regards,
- Tehran, Iran
A. Dear Ms. Abiri:
a. If you do not use grain refiner before the phosphating stage, you won't succeed to overcome the 24h Oily phosphating requirements.
b. 24 Hours salt spray is the requirement of heavy zinc phosphate coating Military standard, the coating weight of the Zinc Phosphate might exceed 10 grams per sq meter. You must check phosphating coating weight to see if you fulfill the requirement.
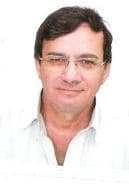
Yehuda Blau
YB Plating Engineering and Quality - Haifa Israel
A. If iron containing a 1:1 ratio of phosphate:nitrate is OK. For accelerated baths raise 1:2 to encourage autocatalysis of the nitrite accelerator. Your nitrate content is far too low. Careful with Cu as over-addition will adversely affect corrosion resistance. Just stick with nickel!
Roger Bridger- Croydon, U.K.
Q. Dear Mr Bridger,
Many thanks for your answering. unfortunately we cannot understand the meaning of 1:1 and 1:2 each ratio refers to which component in the phosphate solution? Which section is in the phase and which one is in denominator? Any information on this topic will be greatly appreciated.
Thanks and best regards,
- Tehran, Iran
A. Hi again!
The nitrate content is usually higher than the phosphate content. At 70 °C some nitrate will produce nitrite autocatalytically and prevent the process building up in ferrous iron. If the process switches over from nitrite containing to iron, higher temperatures and longer process times will be needed to produce complete coatings, which will be of a higher weight.
As an example of ion contents for a 20 pt bath:
Zinc 6 g/l phosphate as P2O5 8 g/l Nitrate as NO3 15 g/l
Cheers,
- Croydon, U.K.
A. Dear Ms. Abiri,
How do you do the "Salt-Spray" test? with or without primer (E-Coat, powder,...)?
As you know doing "Salt-Spray" test only on phosphated plates is meaningless!
You should do another test methods such as: "Cyclic Corrosion" test, "VDA",...
Best Regards,
- Tehran, Iran
March 3, 2009
A. Dear Ms. Sara. You had better use low zinc phosphating solution.
Reza Moumivand- Tehran, Iran
March 15, 2012
A. To respond to the first question, your formula is missing a calcium additive. Read up on the advantages of Calcium modified Zinc Phosphate processes.
Andre De Graaff- South Africa
July 13, 2016
Free acid vs. total acid
Q. dear sir,
I am a paint technologist working in India. I have confusion between the free acid and total acid.
I would like someone to describe to me what does it mean the free acid and total acid, and how can I adjust the ratio of free acid to total acid at particular point. Also in the phosphating process what happens when "free acid:total acid" ratio changes.
Best of all,
PAINT SHOP EMPLOYEE - VADODARA, India
2007
A. Dear,
FA, TA are important factors in zinc phosphating. FA is 0.6 to 1 point, TA is from 14 to 22
- 10th Ramadan, Egypt
Cold Phosphating Formulation
Q. DEAR SIR , I AM INTERESTED TO MANUFACTURE COLD DIPPING ZINC PHOSPHATING CHEMICAL BUT RESULT OF MY SAMPLE IS VERY POOR IN TERMS OF COATING , PLEASE ADVICE ME FOR HEAVY CRYSTALLINE COATING . RESULT FOR CORROSION TEST IS O.K. I AM USING PHOSPHORIC ACID 85% (14 G/L) , ZINC METAL (3.5 G/L), MN (.564 G/L), HNO3 60% (3.250 G/L) AND NANO2 AS ACCELERATOR ABOUT 0.25 G/L .
NITIN PATELMANUFACTURER - VADODARA, GUJARAT, India
June 12, 2009
A. Dear Mr. Nitin Patel,
There are two problems is in the formulation:
1. The basic percentages in the formula are imbalanced.
2. For cold phosphating additional chemicals are required to be used to give the bite in the absence of the heat.
Regards.
- Chennai, Tamil Nadu, India
Q. DEAR SIR ,
I AM INTERESTED TO MANUFACTURE COLD DIPPING ZINC PHOSPHATING CHEMICAL BUT RESULT OF MY SAMPLE IS VERY POOR IN TERMS OF COATING , PLEASE ADVICE ME FOR HEAVY CRYSTALLINE COATING . RESULT FOR CORROSION TEST IS O.K. I AM USING PHOSPHORIC ACID 85% (14 G/L) , ZINC METAL (3.5 G/L), MN (.564 G/L), HNO3 60%.
- NOIDA (U.P.) India
December 13, 2010
A. Dear Mr. Praveen,
The problem is in the ratio of the basic ingredients. Please inform what is the percentages you are working with.
Regards.
- Chennai, India
⇦ Tip: Readers want to learn from your situation;
so some readers skip abstract questions.
Q. I want to know the composition of zinc phosphating material used for pre treatment in powder coating.
Vijaya SountharPowder Coating - Coimbatore, Tamil Nadu, India
June 3, 2011
A. Hi, Vijaya
As you can see, we appended your inquiry to a thread which may already answer it for you. But please introduce yourself and your situation and then follow up if you have remaining questions. Thanks.
Regards,
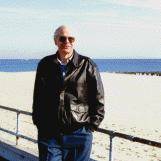
Ted Mooney, P.E.
Striving to live Aloha
finishing.com - Pine Beach, New Jersey
A. Dear Mr. Saunther,
The composition includes Phosphoric Acid and Zinc.
- Chennai, India
⇦ Tip: Readers want to learn from your situation;
so some readers skip abstract questions.
Q. Hi, I just want to know how I can make fine grain phosphate formulation, because the coating presents white powder after finish, and the customers they prefer dark finishing.
Thanks
- Montreal, Canada
December 13, 2011
A. Hi, Francisco
I don't think people will be able to guess the details of your current formulation solely from the fact that the result is white. If you want suggestions for improving it to a darker color, I think you'll need to say what your formulation currently is. Thanks.
Regards,
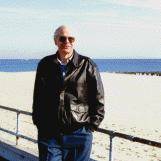
Ted Mooney, P.E.
Striving to live Aloha
finishing.com - Pine Beach, New Jersey
Rust on inner surface
Q. HI ALL,
I'm recently finding red rust in the inner surface of upper part of iron metal after zinc phosphating. We are using hot phosphating manually. Can anybody help me to sort out this problem?
- Bangalore, Karnataka, India
January 6, 2013
A. Hi Chikki. I'm not understanding what you mean by the inner surface of the upper part, but is trapped air preventing the phosphatizing and other solutions from reaching that area? If you are seeing any rust shortly after phosphatizing, that area has probably not been phosphatized.
Regards,
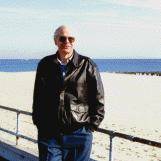
Ted Mooney, P.E.
Striving to live Aloha
finishing.com - Pine Beach, New Jersey
A. Hi Chikki,
Like Ted, I am not certain exactly what you are doing, but you do need to beware that zinc phosphating on its own will not prevent corrosion, the coating is a discontinuous crystalline coating and tends to be used for a base to paint, bond or put on some other type of supplementary coating.
If you are seeing immediate flash rusting then Ted may well be right and you are not getting complete coverage, possibly due to air entrapment. It may also be the fact that the surface is remaining wet for too long, so you aren't getting things dried before flash rusting starts, also if the rinsing is not sufficient the cold phosphate solution will also promote corrosion.
If you are seeing the rusting occur after a period of time it will be because the supplementary coating is not being applied in time or no supplementary coating is being applied at all.
Aerospace - Yeovil, Somerset, UK
Q. Can anyone help with the Cold Phosphating process, I need to know what chemicals are needed and the application.
Bosco Arokiaraj- Trichy, Tamil Nadu, India
April 19, 2013
Q. Could you give me the permissible limits of the following parameters with respect to Zinc phosphating bath:
1) percentage of oil content in Acid Degreasing bath
2) percentage of iron content in Phosphating Bath
3) free Acidity of a phosphating bath operating at 28 ml pointage.
4) iron content in Derusting Bath
Thanks
- Mumbai, Maharashtra, India
August 13, 2013
A. Hi cousins. Please take this charitably -- my intention is to help you get the assistance you seek by telling you what I've learned by curating hundreds of thousands of Q&A's posted on this site for decades: please fully present the specific problem you are having, YOUR ACTUAL SITUATION!,
When questions are cast in the abstract, readers rarely answer: firstly, abstract questions involve a dozen ifs-ands-&-buts that don't apply to your situation but can't be skipped without misleading other readers; secondly, flashcard-style quizzes give the impression that you want others to rifle through textbooks and provide summaries because you can't be bothered yourself; finally, readers can help you resolve a specific situation, but can't instantly elevate others to where they become experts themselves, able to independently solve more generalized problems.
Thanks & Regards,
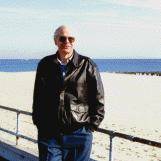
Ted Mooney, P.E.
Striving to live Aloha
finishing.com - Pine Beach, New Jersey
⇦ Tip: Readers want to learn from your situation;
so some readers skip abstract questions.
Standard phosphate coating
Q. In standard phosphate coating after HCl pickling and washing, what should the concentration of phosphating solution be?
Indu Indukumarquality - Bazpur, Uttrakhand
September 13, 2013
⇦ Tip: Readers want to learn from your situation;
so some readers skip abstract questions.
Q. Hi,
My name is Hassan. I was searching for how to make a solution for hot and cold phosphate coating for pre-paint treatment for iron and I came across this forum. Can someone help me regarding this.?
Student - Lahore, Punjab, Pakistan
February 23, 2014
A. In zinc phosphate coating when I use zinc nitrate and phosphoric acid it works well; but when I use zinc oxide and nitric acid instead of zinc nitrate it doesn't work. I don't understand why anyone says use zinc oxide and nitric acid.
Ali shafizadeh- iran esfahan
A. Dear Shafi:
Zinc oxide is used in the formulation. It reacts with phosphoric acid to make zinc phosphate. Zinc nitrate is not required.
- Chennai India
October 29, 2015
Phosphating bath Free Acid is dropping after filtration
Q. Hi, I am umesh. We are powder coaters. We are having seven tank pre treatment line. Recently we installed a online sludge separation filtration system. It is working fine. It is separating sludge and keeping the bath clean. But we are facing a different problem. We are noticing that, after filtration, the Free acid level is dropping drastically. Bath temp 45-50, dip phosphating, 6000 ltr bath size, 5000 sq.m/day. Could anybody tell me why this is happening. What is to be done to avoid this.
umesh kulkarnibuyer - Pune, Maharashtra, India
March 23, 2015
A. If you are maintaining tank level control, then the reason would be that water is being added to make up for the volume of sludge that has been removed. This will dilute the bath and cause FA to drop.
Dan Mack- Horicon, Wisconsin
Will nitric acid addition correct low free acid in zinc phosphate bath?
Q. Dear sir,
What happens if I will add 500 ml of nitric acid to a 12 kl zinc phosphate bath, as we facing some issues due to low F.A of our bath, and I think with nitric acid F.A will increase? I want to know if there is some issue with it or not.
tube draw process - chandigarh, India
May 8, 2015
Surface finish
Q. I have a very crucial information about this.
But I want to be more clarify .
So my parts are getting pinhole defect
And obviously they are found at unloading station.
My process parameters all are in medium range.
So it could be in phosphate process will be developed.
I want to troubleshoot this very immediately
- Pune India
September 19, 2015
A. Hi Revan. Sorry, I've never heard of pinhole defects in zinc phosphating, but I'm not sure if I am quite understanding you. Unfortunately, telling us that everything is in mid range, i.e., that there is nothing wrong, isn't really very helpful because obviously something IS wrong.
It sounds to me like either your cleaning isn't working or you are generating loads of hydrogen gas for some reason. If you have additional detail, or pictures, perhaps a reader can help. Good luck.
Regards,
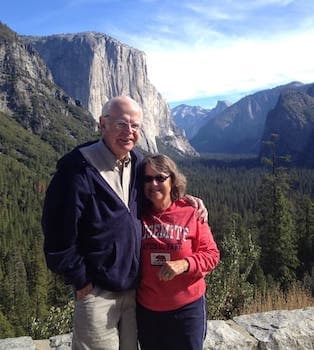
Ted Mooney, P.E. RET
Striving to live Aloha
finishing.com - Pine Beach, New Jersey
Q. Sir I had used it to coat galvanised iron straps, so this problem occurred on this part only ...
Revan Rustampure [returning]- Pune India
A. Hi again, Revan. Zinc dissolves extremely rapidly in acids. Are you putting these galvanized straps through the same acid dip which you use to activate steel parts? That will certainly cause pinholes in the galvanizing if not completely destroy it.
Regards,
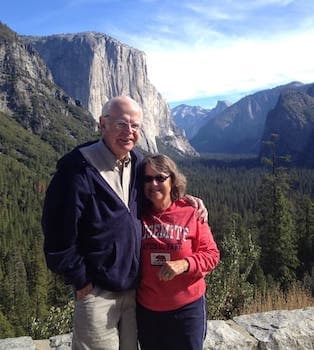
Ted Mooney, P.E. RET
Striving to live Aloha
finishing.com - Pine Beach, New Jersey
How to decrease zinc phosphate coating weight on steel
Q. We are using zinc phosphate for coating in our pickling process.
The issue is that we get a coating weight about 150 mg /ft^2 higher than the standard specs. Could you suggest a method so that we can decrease this wastage ?
student - Ranchi, Jharkhand, India
May 26, 2016
? Hi Ojas. What is your zinc phosphate formulation? Are you dipping or spraying? What coating weight are you shooting for? Thanks.
Regards,
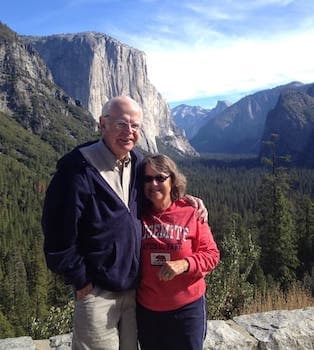
Ted Mooney, P.E. RET
Striving to live Aloha
finishing.com - Pine Beach, New Jersey
Q. Hi Ted
We are willing to achieve a coating weight of 600 mg/ft^2 but are getting a weight of around 730 on an average
We dip the steel into phosphate solution
The formulation of solution is as follows -
Zinc content 9-10
Phosphate content 20-24
Total Acidity 40-48
Kindly suggest a method to reduce this coating weight to desired around 600
We want to reduce this large wastage so please guide us to what can we do regarding the operating temperature of dipping tank, time of dipping, concentration, etc.
- Ranchi, Jharkhand, India
A. Hi Ojas. Thank you for the data.
I was asking for it as the site curator because I felt it would be hard to go further without it. I am not actually a zinc phosphating expert, but my limited understanding of zinc phosphating (pending a better answer from another reader) tells me that efforts toward reducing grain size will reduce coating weight -- so please see Yehuda's suggestion above. For further detail on activator/grain refiner please see topic 14221, "Surface Activation for Phosphating. Grain Size Issues", especially P.M.Saravanan and TSN Sankara's outstandingly informative entries. Good luck.
Regards,
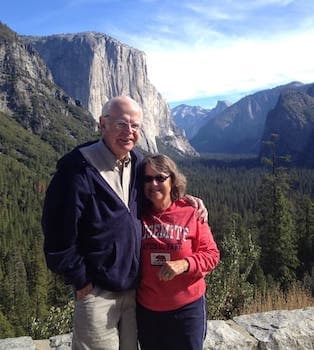
Ted Mooney, P.E. RET
Striving to live Aloha
finishing.com - Pine Beach, New Jersey
A. Hi Ojas!
The Zinc Phosphate solution to be used should be 3 % in water and maintain a temperature of 70 °C.
If you are coming with your own formulation then share it so that it can be corrected.
Also add Titanium based salt bath before phosphating to give fine etching and hence finer and low weight coating. The adhesion also will be excellent.
Please try this and share the results.
- Chennai, Tamil Nadu, India
A. Hello,
My advice would be to use a grain refiner; this may be enough to get you to within your limits alone if that is not enough reduce the time in the phosphate bath until you get within your range required. I have just been doing a project on some small base plates and managed to achieve 3-5g M2 using a grain refine and only 1 minute in the zinc phosphate after 2 1/2 they were fully phosphated and I was achieving 17g M2 !!
Surface technology - Leeds United Kingdom
Q. How to improve quality of Zinc Phosphating? Can anyone sort out my problem ?
Currently we are using Hot Phosphating process (75-80 °C). Mainly we are facing problem for Mild steel, EN 8, EN9, EN 19 & EN 24 material.
After phosphating & oil sealing, around the surface bottom side we are getting very rough coating while at upper side we are getting smooth coating. Also after phosphating, approx. 6-8 months we observed rrddish colour and are required to rephosphate.
I want to update preservation methods of phosphatised components and formulation of phosphating solution to achieve smooth and linear coating.
- Pune, Maharashtra, India
October 6, 2016
A. Hello Pradeep!
Please tell us more about your process:
- Is it a barrel process?
- How do you process the parts? (degreasing, how many rinses, pickling, how many rinses, phosphating, how many rinses, sealing?)
- What shape are the parts you process?
I think we can help you if you tell us more.
Regards!
Daniel
N FERRARIS S.A. - Cañuelas, Buenos Aires, Argentina
How to maintain the Total acid and Free acid ratio in Phosphating process?
Q. Dear Sir,
How to maintain Total acid and Free acid ratio in case of Zinc Phosphating process .
To lower the FA , caustic may be added but in that case TA will be decreased also. So please suggest how to maintain the ratio.
Thanks and regards.
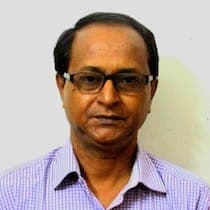
Rathin Mukhopadhyay
- Kolkata, West Bengal, India
October 24, 2016
A. Hello Rathin!
Do you formulate your own bath? If not, you should ask your vendor, as the products are balanced to mantain the relation between FA and TA in the operational values.
If you are formulating your own bath, my advice is to add one formula to replenish the drag-out and one formula to mantain the TA in process (adding product by parts/barrels/racks processed). The second formula should have more FA than the first one to mantain the relation. There is no magical formula, you should try and adjust it until you have the one that mantains the relation in your optimum range.
Hope you can solve your problem! Regards,
Daniel
N FERRARIS S.A. - Cañuelas, Buenos Aires, Argentina
Q. What ratio will have to take zinc nitrate and phosphoric acid? Other question: in phosphating we are using zinc nitrate and phosphoric acid; does it need further coating for sodium nitrite as accelerator? What composition do we have to make it for good coating?
Suganya sambath- Chennai, tamilnadu and India
February 20, 2017
⇦ Tip: Readers want to learn from your situation;
so some readers skip abstract questions.
Q. Hi. Can you please tell me formulation of zinc phosphate?
How can I make one Zinc phosphate Drawing liquid?
student - TEH, IRAN
March 17, 2017
A. Hi Ali. Although the page may be confusing, the answers are here, very insightful answers.
Because the thing is, it's easy enough to make a zinc phosphating solution with nitric & phosphoric acid and zinc oxide, but what most users are actually seeking is the composition which will work best for them in terms of corrosion resistance, salt spray, grain size, undercutting prevention, paint adhesion, minimal sludging, robustness against small process variations, freedom from toxic ingredients ... and which will work on their steel, cast iron, zinc, and aluminum products ... and will be inexpensive.
Thus the page introduces the ideas of controlling total acid vs. free acid, employing additional ions like calcium and nickel, and grain refiners like titanium, and accelerators, etc. In the West these days, shops do not try to formulate their own zinc phosphating solutions, but purchase proprietary formulations which are the result of decades of research into all those factors. Good luck.
Regards,
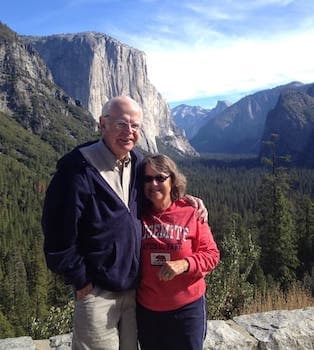
Ted Mooney, P.E. RET
Striving to live Aloha
finishing.com - Pine Beach, New Jersey
Q. Hi there!
I'm facing this situation: Currently my Zinc Phosphate bath is not stable. The Total Acid and Free Acid is completely out of the range and their values are 50 and 3 respectively. I've tried to lower down the values by adding the Additive as provided by the supplier but still couldn't help.
Can anyone help me? Any advise? Please =(
- Pulau Pinang, Malaysia
July 15, 2017
A. Dear,
It is recommended to add Di water in your bath about 50% to reduce 50% of your bath values. Then add about 20% sodium hydroxide aq sol in phosphate bath to adjust the free acid in between 0.6 to 1.0.
- Lahore- Pakistan
April 23, 2024
⇦ Tip: Readers want to learn from your situation;
so some readers skip abstract questions.
Q. Hello sir. I want to prepare zinc phosphating chemical, so which other chemicals are used with phosphoric acid?
Parag khatsuriya- vadodra,gujarat, India
October 6, 2017
A. Hi Parag,
There are many many formulations for many many different uses, and there are a large number of vendors offering proprietary formulations that no one but them can tell you that formula.
I think that if you want to use a zinc phosphate bath, you should buy some proprietary phosphate from a vendor. If you want to sell a phosphate as you product, you should make your own formula by experimenting and getting information from old patents or some actual phosphate producer.
Hope you can make something of this recommendations! Best of lucks!
TEL - N FERRARIS - Cañuelas, Buenos Aires, Argentina
Q. Hello sir I am from Delhi, India .
Can you tell me please how to make cold phosphating chemicals for grey colour coating on iron sheets by dipping process & also tell how to balance free acid and total acid?
Employee - greater noida, India
November 11, 2021
A. Hi Santosh. Regarding free acid vs. total acid, if you don't quite understand the discussion on this thread, then thread 47351, "Free and total acidity in phosphating vs. salt spray performance", and thread 31949, "Zinc Phosphating process control & analysis" may help clarify the subject.
There are several good books that will tell you what is involved in phosphatizing chemistry, including Biestek & Weber's "Conversion Coatings", Rausch's "Phosphating of Metals"
⇦[this on
Amazon
or
AbeBooks affil links], Samuel Spring's "Preparation of Metals for Painting", and Freeman's "Phosphating & Metal Pretreatment"
⇦[this on
Amazon
or
AbeBooks affil links].
Or you can do a search through patents.google.com to see what people claim are the critical elements, or scholar.google.com to see what researchers have determined.
Luck & Regards,
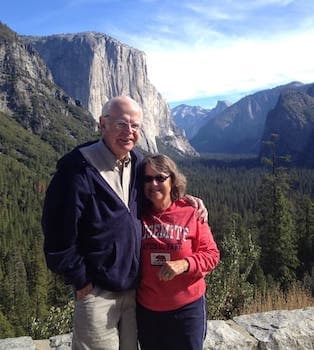
Ted Mooney, P.E. RET
Striving to live Aloha
finishing.com - Pine Beach, New Jersey
Q. Anyone tell me please how to make 3 in 1 chemicals for metal pretreatment process?
Santosh kumar Yadav [returning]Employee - greater noida, India
Q. Hello everybody.
I'm a car and motorcycle restorer, both bodywork and mechanical.
What I'm searching is a simple recipe for a zinc phosphate solution, to spray cold (possible without rinsing, but I think that I'm asking too much).
I only have access to zinc (pure anode and similar), zinc oxide
⇦ on
eBay or
Amazon [affil links]
and a cleaning product with 50% + Phosphoric Acid.
[I did go around this useful site (and not only), and found a couple of recipe that I tried (using only what I can get).
Where I live there are no ready-made product].
Thanks.
I written maybe too much
- Lombardia, Italy
May 7, 2022
by Biestek & Weber
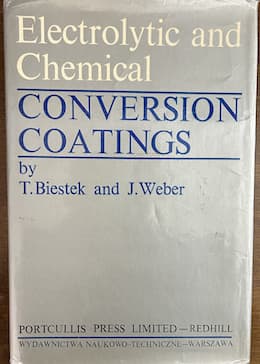
on AbeBooks
or Amazon
(affil link)
A. Hi MickIT. There are hundreds of readers for every poster, and we don't want them lost or misled so bear with me if you already know this stuff ...
Although the phosphating step per se is a single step, the overall zinc phosphating process is usually 7 steps. So once you have the formula you still need to do the other 6 steps as well, which include alkaline cleaning, acid activation, grain refinement, and passivating rinse.
In the developed world it's quite unusual to try to formulate your own solutions; the process is usually bought from a supplier who markets the process as a proprietary. Rather than asking a licensing fee, they recoup their R&D costs 'by the gallon'.
Biestek & Weber (in the unlikely event you can find it) has a 6-page subchapter just on room temperature phosphating. According to that source the ideal zinc concentration is 22 g/l, but the pH must be held within a 0.1 range, but the required pH varies depending on the exact temperature, and is probably somewhere around 2.7; if zinc oxide can't keep it from dropping, sodium hydroxide in the form of drain cleaner is surely available. Commercial products also contain accelerators of nitrate + nitrite, chlorate, or copper salts, and significantly higher concentrations are suggested for cold phosphating than for hot.
It may not be possible to formulate a successful zinc phosphating solution from just zinc, zinc oxide, and phosphoric acid -- it might be better to do simple iron phosphating, which requires nothing behind a good cleaning and phosphoric acid :-)
... but we've appended your inquiry to a thread which offers several people's formulas.
Luck & Regards,
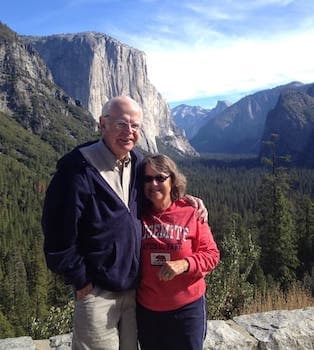
Ted Mooney, P.E. RET
Striving to live Aloha
finishing.com - Pine Beach, New Jersey
Q. Hello. Thanks for your answer.
I think you described the industrial coating (car parts used to have that, maybe guns?), done in big tanks.
What I was talking about is the spray restorers usually apply after sandblasting, prior to painting.
It's just a clear liquid.
What some people suggested is to mix simply phosphoric and zinc.
But as said, I've never obtained the right ratio between the 2 components.
Best regards
- Lombardia, Italia
A. Hi. Apparently 22 g/l of zinc is a pretty good number, but I'm not finding evidence in the literature that a useful zinc phosphatizing solution can be formulated from just zinc, zinc oxide, and phosphoric acid --let alone a room temperature process.
Without zinc added you would be doing phosphoric acid cleaning, which is of some value. Unless you can produce for yourself some evidence (adhesion tests, accelerated corrosion tests, etc.) that someone's addition of some amount of zinc improves things over straight phosphoric acid, my guess is that it doesn't :-)
Luck & Regards,
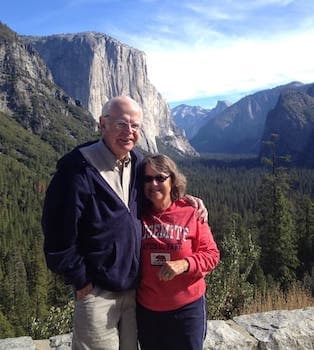
Ted Mooney, P.E. RET
Striving to live Aloha
finishing.com - Pine Beach, New Jersey
Can't phosphate high carbon steel
Q. We are facing problem in phosphating on EN19 material. Some parts are found gray and some parts found black in a single batch. Problem is found only on EN19 material which is high carbon steel material. Other metals found Okay. Please suggest how to resolve it?
Raju PatelOwner - Ahmedabad, Gujarat, India
May 21, 2022
A. Hi Raju,
Without being told anything about your phosphating process, there are a lot of "ifs-ands-&-buts" to make much progress, but according to Biestek & Weber, for non-accelerated solutions, "alloy constituents of steel give rise to tremendous differences in the formation of coatings ... poor coatings are also produced on steels containing certain carbide forming elements, for instance chromium ..."
I think the short answer might be that if you are presently using home-brew phosphating solutions, you should perhaps either only phosphate low carbon steel or consider switching to a proprietary :-(
Luck & Regards,
Ted Mooney, P.E. RET
Striving to live Aloha
finishing.com - Pine Beach, New Jersey
A. DEAR SIR,
The colour difference is due to the carbon coming out from the EN16 material while pickling.
Method-1
If the acid concentration is high, you will not get uniform coating.
So you have to find out the suitable operating concentration with respect to the dissolved Iron content.
Keep the excess time in pickling rinse-1 until the components looks uniform.
Then requested to do the process.
Method-2
Please add the complex fluoride in the phosphate bath to 800 to 1500ppm.
- CHENNAI
June 19, 2024
Q, A, or Comment on THIS thread -or- Start a NEW Thread