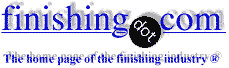
-----
Salt Spray Standards - What do they really indicate?
Q. Many states have performance based specifications for pipe products that contain specific hours of exposure to salt spray before 5% red rust, for example 300 hours or 650 hours. How and why were these levels arrived at? What is their actual relevance to actual performance? Would 650 hours in this situation indicate performance at a level over twice as good as 300 hours?
Joseph San Georgetubing mfgr. - Phoenix, Arizona, USA
A. Hi Joseph,
Salt spray exposures don't correlate to real-world performance. It would also be incorrect to infer that a part that lasts 600 hr in salt spray will last twice as long in real service as a part that lasts 300 hr.
I don't know how people come up with salt spray specs. A dartboard is as good a guess as any!
George Gorecki- Naperville, Illinois
A. This is one of the oldest questions in the book and the answer is that salt spray hours do not correlate to real-world exposure in any quantifiable way. Salt spray hours are simply a general measure of quality: if the parts are not processed right, they will not pass the salt spray test, and those parts PROBABLY would not have done well in the real world.
But it's not going to be a matter of a few hours of salt spray one way or the other. You are not going to find parts lasting 297 hours but not 300 hours, or 650 hours but not 660 hours.
As for why one standard vs. the other, that too is pretty much empirical. If the spec was originally for 300 hours and then it was discovered that parts which passed this test did not exhibit the desired real-world life, the spec would be changed; it would pointless to marginally adjust it to 310 or 315 hours, so a big jump would be made to something like twice the number of hours.
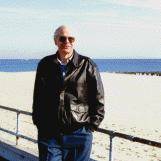
Ted Mooney, P.E.
Striving to live Aloha
finishing.com - Pine Beach, New Jersey
Q. ASTM B117- 94/97 is merely an indication that the tested parts will corrode in seacoast or seagoing environments. If corrosion is of concern - i.e. structural or chemical potential failure - then salt spray is very useful.
I would be interested in other's opinions as to determination of effect of salt spray on parts. Much of our time is spent evaluating plastic coatings, much like paint, compared to painting.
Here is ours: salt spray is filtered of 'rust' i.e. solids, before recycling the salt solution (typ 20%); parts after trial, typically 240 hours, are washed, wiping with soft cloth careful to not remove any corrosion, dried; examined carefully for 'rust' or corrosion, even using 50x micro.
And of course, change in weight. The 'amount' of rust/corrosion is graded 1 to 10 to assess the level of risk on a 30 year life. Comments are appreciated. Thanks.
Warren J Pegramplastic parts - Snow Camp, North Carolina USA
A. Hi, Warren. It would be great if you could predict risk over a 30 year life via a salt spray test, but I don't feel it actually has any validity at all. For example, there is probably no finish that offers the corrosion resistance of hot-dip galvanizing. Galvanized towers and other structures can last 75 years and even more with minimal maintenance. And why is that so? It's because the zinc will sacrificially protect the steel, so the steel doesn't corrode until the zinc is gone. But why doesn't the zinc coating itself rapidly corrode away? Because it reacts with the carbon dioxide in the air, forming a skin of zinc carbonate reaction products that are hard, tenacious,glassy, impervious, and greatly reduce further corrosion of the zinc. But this reaction occurs only in the open air over years -- galvanizing performs very poorly in salt spray tests.
Regards,
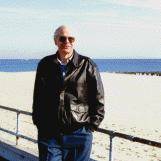
Ted Mooney, P.E.
Striving to live Aloha
finishing.com - Pine Beach, New Jersey
October 23, 2010
January 11, 2011
Q. Hi,
I'm working to create some standards of coating types here in the company. For now, I defined a 'chemical nickel', a lamellar zinc and some alloy zinc coatings. I still need an electrophoresis paint (like E-coat).
Usually, we define a thickness of 8-12 micro m and (at least) 96 hours of salt spray test without coating corrosion (or 'white rust') and we 'hope' that it will guarantee at least 5 years (in a city environment) in the same condition - with no coating corrosion.
So, my question is, is there some relation of salt spray hours test and big cities typical environment?
And is there some standard (or book, or any bibliography) which defines the thickness vs. the salt spray test hours?
Thanks in advance
Ivam
product designer - Sao Paulo, Brazil
A. Hi, Ivam.
Salt spray testing is a quality assurance test, not a predictor of real life. Unfortunately, it is particularly inapplicable to use such testing to compare one type of coating against another. One of the reasons is that corrosion products tend to protect the substrate from further corrosion but the corrosion products that are formed in salt spray testing are fundamentally different than the corrosion products formed in the real world, so the results are different. Some coatings that excel in the real world perform poorly in salt spray cabinets and vice versa.
Further, the protection mechanisms of the three coatings that you are talking about are utterly different. Chemical nickel is very corrosion resistant, but if a small nick or scratch develops, the fact that nickel is cathodic to steel means that the coating will accelerate the corrosion of the base metal. Zinc and zinc alloys are anodic to steel and will protect it from corrosion even if the coating is scratched. Electrophoretic coatings comprise more classical barrier layers that neither accelerate nor retard corrosion of the substrate if the coating is compromised. Although their are numerous accelerated corrosion tests like CASS, Corrodkote, Sulfur Dioxide, that are considered better than ASTM B117 for specific combinations of substrates and coatings, the general problem prevails. Good luck.
Regards,
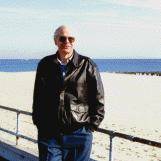
Ted Mooney, P.E.
Striving to live Aloha
finishing.com - Pine Beach, New Jersey
January 12, 2011
January 12, 2011
Thanks Mr. Mooney.
So, it makes sense with the test which my chemical nickel's supplier suggest me - the ferroxyl test - because it (should) find any possible crack or small nicks at the nickel layer.
Thanks again, for the fast answer!
best Regards!
- Sao Paulo, Brazil
----
Ed. note: Letter 12752 discusses the use of the ferroxyl test on electroless nickel coatings.
Should screw threads be exposed or protected for salt spray test?
Q. For the salt spray test should I protect the threads for a screw? It is coated with zinc.
Gonzalo Soledad- El Paso, Texas
November 27, 2013
A. Gonzalo,
I think that's a question to ask your customer. Since only the head of the screw will be exposed to the environment, perhaps that is the only part they care about. Or perhaps they want to evaluate the entire screw. If the zinc coating is uniform, it shouldn't really matter, the threads should perform as well or as poorly as the head does anyway.
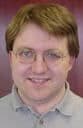
Ray Kremer
Stellar Solutions, Inc.

McHenry, Illinois
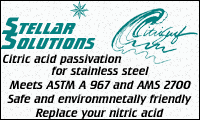
December 3, 2013
Q. Hi I want to know that if we've done salt spray test on zinc plated material for 72 hrs., then no spot of rust we find, can anyone tell that after how many days rust will form on that particular component.
Ravinder Kumar Pathania- chandigarh Punjab India
November 21, 2016
A. Hi. This test tells you that rust won't form in 3 days, but that's about it. Salt spray testing, especially of zinc plating, is completely unrepresentative of real life and is not intended to predict real life. Rather it is a QA measure: if the parts have been found to perform satisfactorily and also to last 72 hours in salt spray ... and then they start failing in 72 hours, something has probably gone wrong which will reduce their satisfactory real life.
By the way, 72 hours is not a high standard at all for zinc plating. Good luck.
Regards,
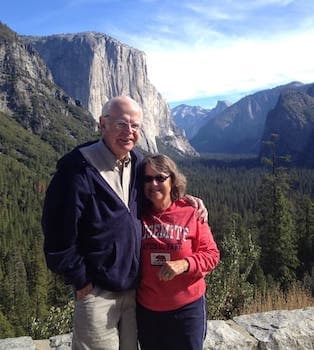
Ted Mooney, P.E. RET
Striving to live Aloha
finishing.com - Pine Beach, New Jersey
November 2016
Q, A, or Comment on THIS thread -or- Start a NEW Thread