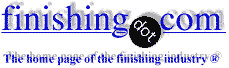
-----
Finishing Aluminum Castings: burrs / flash / lamination issues
2002
Q. I am looking for a finishing process that will remove flash, burrs, lamination from aluminum die castings. A trim press is used to remove large window flash, but many areas require subsequent processing to remove sharp edges from internal cavities. The current method utilized is a person with a steel file (after the parts are shot blasted). It is very ineffective. Pneumatic hand tools have been used in the past but part geometry inhibits effective processing.
Are any of the following processes applicable?
chemical wash
high pressure water blasting
thermal deburring
vibratory deburring
others?
- Indianapolis, Indiana
A. There are too many unknowns here to answer your question properly. Because you mentioned the use of a hand file, the alternatives you suggested did not sound aggressive enough. Part size, volume of pats, configuration or accessibility as well as what is the final surface finish are all important to answer this question.

AF Kenton
retired business owner - Hatboro, Pennsylvania
2002
Q. The parts in question are high-pressure-cast aluminum transmission cases and converter housings. Part geometry varies widely by product line. Generally speaking, the trouble areas are oil passageways that pass through the casting. Typically 1/2" square and entering 2-3" from the face of the part. This passage intersects with a similar passage entering from an adjacent face of the casting.
The interior passage has flash at the deepest point of the passage (where the two die surfaces mate during casting). A punch press operation ensures that the flash does not completely seal the passageway off, but is not precise enough to ensure 100% flash removal from this intersection point. That's where the hand filing commences, but with 10-20 discrete oil passages that must each be inspected and "touched up" ... you can imagine the volume of labor that is required to keep up with the flow of parts.
Jason S [returning]- Indianapolis, Indiana
2002
A. Sounds as though it's past time for new dies, so the flash doesn't occur in the first place. You can't make good quality product from worn or badly made tooling.
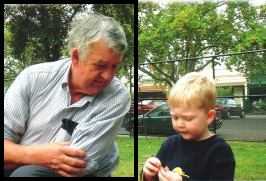
Bill Reynolds [deceased]
consultant metallurgist - Ballarat, Victoria, Australia
We sadly relate the news that Bill passed away on Jan. 29, 2010.
2002
A. It sounds like the part itself eliminates several of your options. The part is probably to large for thermal deburring, and because of the passages you definitely would not want to attempt vibratory deburring. It is hard to say without seeing the part but, have you thought of brush deburring. It may require Robotics and or fixturing, but if the volumes are high enough it could be justified.
Arnold Walker- Independence, Kentucky
2002
2002
A. Typically the options you outlined are options as follows:
1.Thermal de-burr is for small sized castings because of the chamber size and competitive pricing means filling it up to the top; Also, a thermal de-burr is good for this type of flash as you have described but the casting sounds too big.
2.Chemical mill is much more effective on zinc and for much thinner flash ( approx. 0002"-.008").
3.Vibratory de-burr could work, but needs the internal core (where the flash is)to be of a size so the media doesn't get stuck in the casting interior; Additionally, if the flash is too heavy, it just rolls it over,causing more of a problem. Also, the castings may be too large for the mills; Common mill size is from 6-10 cubic feet.
4.A small de-burring tool is probably the most plausible solution if the castings are too large for the above options; A good solution is a miniature air driven belt sander that allows the operator to go into the casting and eliminate the flash from the intersecting cores,but if the flash is too thick, it will tear up the belts, and be quite expensive and time consuming......so, files may be your only option besides fixing the tooling.
Joe DeAmicisdie casting & plating - Edison, New Jersey, USA
A. Sorry it took so long to get back to you, but you got some good responses. My best suggestion is to look into abrasive honing or extrude hone technology. This is an expensive system, but it is probably the best suggestion I can come up with.

AF Kenton
retired business owner - Hatboro, Pennsylvania
2002
A. There are rotary disc type brushes that can be custom designed for de-burring, they are an abrasive nylon filament impregnated silicon carbide. These are typically used in a variety of applications for de-burring.
Michael A. Ruffalo- East Point, Georgia, USA
2003
Aluminum Casting Surface Finishes
Q. I have customers whom want a polished surface.
We are currently casting in an alloy contain 9% Mg. The final product appears with a colour variation over the surface. In some areas the colour is very dark.
What is the reason for this "colour" variation?
After polishing they seem to disappear, but after surface treatment, these colour changes appear again.
Are these areas due to variation in composition?
- Birkeroed, Denmark
2006
Q. I have been making Aluminum Alloy Castings For various applications. The Castings are meeting my customer's requirements in form of Quality of Castings, their functional requirements such as Radiographic standards, Hydrostatic requirements, Machining Tolerances,etc.
But when it comes to Surface finish, the castings give a repulsive feeling to my customers. Generally the Castings are made in Aluminum Alloy LM25 & after Heat- Treatment, They assume Grey colour. Whereas the customer wants natural Aluminum colour which could be lustrous. Similarly, I am also making Castings in Alloy LM6. These castings are not Heat-Treated, But nevertheless the customer wants good surface finish on the Castings.
My question is how do I achieve good finish on the castings so that my customers feel attracted to my product.
- HYDERABAD, A.P. , INDIA
2006
A. For Americans, LM6 is ~equivalent to A413, with ~12 wt% Si as the predominant alloying element.
LM25, with 6.5-7.5 wt% Si, is similar to 356 & A356. LM25 has slightly lower limits on other alloying elements than 356, and slightly higher limits than A356.
According to Casting Kaiser Aluminum, 3rd edn. (1974), 356 & A356 "have good polishing characteristics....Anodizing appearance is fair to very good; color is gray." LM25 should be similar, with the gray due to the Si.
A413 & LM6, with about 12 wt% Si, polish poorly. Anodizing appearance is also poor. Plating gives a better appearance.
Do you solutionize the LM25 at 1000 °F (538 °C)? What is the furnace atmosphere used?
How are you currently finishing parts: mass finishing (tumbling or vibratory barrel), bead blasting, polishing..?
- Goleta, California

Rest in peace, Ken. Thank you for your hard work which the finishing world, and we at finishing.com, continue to benefit from.
2006
Polishing naturally pitted [cast] aluminum
Q. I've been polishing the parts for my engine bay. So far I've finished the valve cover and now I am working on the intake manifold. My question is when I polished the valve cover the finish was already smooth; my intake on the other hand has a natural pitted appearance. When I tried polishing it, the Tripoli compound I'm using simply turns black on to the metal. Let me know if there is a solution for this.
Thank you... Joe
hobbyist - Missouri
April 16, 2009
A. Joe,
Cream of tartar works well for removing natural occurring oxide from aluminum. Make a workable paste with cream of tartar & warm water. Apply with a soft brush, and let sit for a few minutes. Wipe clean with warm water and rag. When all the oxide is removed apply a good aluminum polish available at your local auto parts store. This should give you better results.
Fellow Plater - Syracuse, New York, USA
April 22, 2009
A. Polishing out parts that have been polished in the past, such as your valve covers, will usually brighten up using some polishing compound and elbow grease. However a raw sand casting such as an intake manifold will require courser more aggressive materials such as rough grit sandpapers starting with about 150 grit and working down to finer grits (220 then 320,then 600) making sure you get every grit line out from each previous sandpaper. Then try to use a buff with brown tripoli buffing compound
⇦ on
eBay
or
Amazon [affil links]
.
When you use tripoli on a buff before smoothing out a rough casting will result in getting the tripoli pushed into the rough texture of the casting leaving a hard black gunk in the rough texture. It would also help to soak and scrub the casting completely clean with very hot soapy water and a good tampico scrub brush
⇦ on
eBay or
Amazon [affil links] to get any oil and grease out of it. Otherwise you will just clog up your sandpapers and buffs making the job almost impossible.
- St. Louis, Missouri, USA
April 30, 2009
July 17, 2019
Q. Generally, our Castings are made in Aluminum Alloy LM25 / 356 ( Al Si7 Mg0.5 ) . After Heat Treatment, they assume a Grey colour, whereas the customer wants natural lustrous Aluminum colour.
After treatment, we use Steel(SS) ball blasting with 0.4 mm but the appearance remains light Gray only.
What is the method to improve surface finish to silver mill finish?
Working on chemical brightening method at 85 °C with
Orthophosphoric acid (85%) 80 vol%
acetic acid
⇦ on
eBay
or
Amazon [affil links] (glacial, 99.5%) 15 vol%
Nitric acid (60%) 5 vol%
Does this solve the problem of grey color due to silicon, or need any other treatment.
Any solution provider is welcome.
Gravity Casting Manufacturer - Ahmedabad, Gujarat, India
Ed. note: This RFQ is outdated, but technical replies are welcome, and readers are encouraged to post their own RFQs. But no public commercial suggestions please ( huh? why?).
Q, A, or Comment on THIS thread -or- Start a NEW Thread