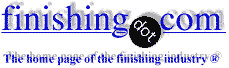
-----
Cadmium vs. Zinc vs. Nickel Plating Comparison
Q. We are currently looking for an alternative to cadmium plated parts. The argument for an "equivalent" to cadmium plate has been going round and round. The parts are threaded assemblies and maintaining tight dimensions is critical to the operation of the assembly.
We were getting a .2 Cadmium plate (commercial grade). The alternatives appear to be Zinc plating or Nickel Plating. Tin-Zinc plating is not an option with our current vendor.
With Zinc, the interaction with metals and the sacrificial nature are issues. The corrosive by-products may cause operation issues in the threads and other tight areas. The base material is SA-1983-B7 Steel.
Can anyone offer any insight to this? The consensus opinion is that Nickel plating offers better corrosion resistance than Zinc. The plater says the Zinc doesn't offer any less protection than the Cadmium plate. I'm just shooting for something comparable to the Cadmium. Any advice/opinions are greatly appreciated.
Brian Bukoski- Erie, Pennsylvania, USA
2002
![]() |
A. Here are two opposites to ponder, Brian: In many cases just switching to zinc will do fine; in other cases it could be a disaster. It depends on how critical the issues I mentioned are. Nickel does not offer sacrificial protection, but sacrificial protection may not be required for your application. Please try to describe it. Thanks! ![]() Ted Mooney, P.E. Striving to live Aloha finishing.com - Pine Beach, New Jersey (Ted is available for instant or longterm help) 2002 A. First, there is no direct equivalent of cadmium. If you have to go away from it, you need to decide what properties you need and in what order or amount of preference. Zinc and cadmium have similar but not equal corrosion resistances. One is better in industrial settings and the other is better in maritime settings. Tin-zinc is the accepted best substitute by most. Nickel offers better corrosion resistance, but has far less lubricity and is not as malleable. You might want to look into some of the other zinc alloys like zinc-nickel, zinc-iron, zinc-cobalt to see if one of those might work as there are a lot more plating shops with those than with tin-zinc. James Watts- Navarre, Florida 2002 2002 A. You would not get the corrosion protection you are looking for from Barrel plated Nickel; your best alternative would be Zinc plate to approx. 4 /10th of a thou and finish with a yellow / iridescent chromate; if the fasteners are any harder than about 28 Rockwell "C" then you might need to consider Mechanical Plating, or plating from a Chloride Zinc solution if the surface is high in carbon & Carbides In most cases Zinc is a better performer than Cadmium in practice however this is not shown in accelerated corrosion testing. Regards, ![]() John Tenison - Woods - Victoria Australia |
A. Brian,
You said that Tin / Zinc is out of the question. How about some of the other alloy deposits such as Zinc / Nickel which seems to be the best of your two worlds, will give you some of the best of both zinc and nickel deposits.
In my opinion Zinc is not as good as Cadmium for corrosion although the chromates are. The nickel deposit will give you superior corrosion but will loose lubricity, nickel deposits tend to be much harder.
It is impossible to replace all the properties of Cadmium with one deposit, but with some research you can get what you have need for.
Chris Snyderplater - Charlotte, North Carolina
2002
A. A finish that will work well for you is Alkaline Zn/Ni 12-16% Ni. This process with a yellow chromate will give at least 1000 hours NSS to white rust and 2500 hours to red rust (assuming 8 microns minimum). The product produces very little in the way of white corrosion products and has excellent slip properties.
Hope that helps.
Regards,
Jonathan Timms- Hong Kong
2002
A. The topic of Cadmium replacement finishes has been ongoing since '95, when the final regulations in the automotive came to light. Many finishes were tested, and very few offer all of the benefits of Cadmium. We just completed a Cad Replacement Study with the US Army, in which our coatings (both chrome-containing and chrome-free versions) were chosen as the best performing alternatives for Cad. They offer most, if not all, of the benefits of Cad, but they are water-based and environmentally friendly. The areas looked at were: cosmetic corrosion, galvanic corrosion (including pit depth and pitted volume), torque-tension (including clampload at 90 ft-lbs, break-loose torque, and torque range), thickness, conductivity and cost. Tin Zinc and Zinc + Yellow were tested in this study and did not compare to the Dacromet(r) and Geomet(r) products. They showed excessive white/red corrosion very early in testing, and there was a large amount of pitting caused by the bimetallic cell (the bolts were tested assembled to an Al fixture). Also, the Army didn't consider Zn Nickel for this study because it did not perform well in their preliminary studies. At the very base of the results of this study was to not consider Zinc Plating + Yellow Chromate as an alternative to Cadmium.
Andrew R. Pfeifer- Chardon, Ohio, USA
2002
!! Thanks Andrew.
Yes, zinc-rich dip-spin coatings are an excellent alternative finish for many applications in both automotive and military. There are several other well-known suppliers of dip-spin coatings including Magni and Dorken. Dip-spin coatings may be the best choice 3 out of ten times or even 7 out of ten times ... but I am shocked that the Army would call them the "best performing alternative for Cad" since most professionals feel that nothing should ever be substituted for cadmium plating except on a case-by-case basis after design review.
The army, if not misquoted here, seems to be implying that dip-spin coated fasteners should be specified as a replacement for cadmium plated fasteners on aluminum aircraft? That sounds like a disastrous mistake; I think only aluminum plating or aluminum Ivadizing are considered satisfactory replacements for cadmium on aluminum airframes. Substitution based on what is best most of the time rather than on a design review is a very very bad idea.
Regards,
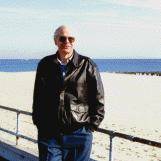
Ted Mooney, P.E.
Striving to live Aloha
finishing.com - Pine Beach, New Jersey
(Ted is available for instant or longterm help)
2002
A. Cadmium is a great corrosion inhibitor, however we're finding that a properly plated piece of iron with tin-zinc outperforms the best cadmium plating job.
Tin-zinc is malleable, offers great ductility and torque characteristics without chipping or flaking off the plated steel part. It offers excellent secondary processing without cracking.
Nickel is terrible for all of the above characteristics and offers poor corrosion characteristics when even compared to plain old zinc.
Remember, for wear protection, hard chrome and nickel are the best. For corrosion protection, zinc and cadmium are the best. If you want ultimate corrosion protection, go with tin-zinc. Zinc-Nickel is okay for corrosion protection but is lacks in secondary processing characteristics. The plating cracks when torquing is applied to the metal part. Tin-zinc usually doesn't.
Roger Fasting- Sacramento, California, USA
2007
Q. I would like to know which coating is better Zinc Coating or Nickel Coating. Which one of the two will provide better corrosion resistance, surface finish.
Bhavneet Singhbuyer - Shanghai, China
2007
A. If one coating were just plain better than the other, nobody would ever use the other, Bhavneet. As mentioned above, the corrosion resistance of zinc will be better in many instances. That's because zinc is anodic to steel and sacrificially protects it, whereas nickel is not anodic to steel but cathodic, so a pinhole or porosity, or a scratch, will lead to immediate failure. But nickel is self-leveling and will certainly give a better "surface finish". Please describe the actual component you are thinking about plating, and then people may be able to give you an assessment based on the function and the environment it will be exposed to. Thanks!
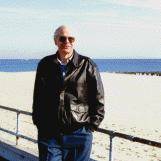
Ted Mooney, P.E.
Striving to live Aloha
finishing.com - Pine Beach, New Jersey
(Ted is available for instant or longterm help)
2007
Q. We are looking for a suitable replacement for the zinc coating found on some of our parts. The reason being is zinc's reaction with Polyamides 6 or 66 (reference GM's Worldwide standard- GMW3044). Would nickel plating act as a suitable replacement as far as friction properties are concerned?
Rick LeslieAutomotive - Troy, Michigan
February 26, 2008
Q. I was wondering what would be better concerning self drilling fasteners (Zinc Nickel or Zinc) - both would come with a top coat, but in your opinion which would serve as a more corrosive resistant undercoat?
many thanks
- Melbourne Australia
August 9, 2010
A. Hi, Donnie
Nickel is primarily a decorative finish. It is a "barrier layer" finish: once compromised by porosity or a scratch, it accelerates the rusting of the fastener.
Zinc is a finish which offers cathodic protection to steel.
While zinc-nickel is indeed an alloy of zinc and nickel, and one might think it's chosen to get "the best of both worlds", that's not quite what it's about. Rather, it's a coating which offers a very specific electrochemical potential so that it cathodically protects steel while not rapidly corroding away itself; plus probably one where the corrosion products are tighter and more encapsulating than plain zinc. So it's a cathodic protection coating intended as a replacement for cadmium or an improvement upon plain zinc. If you are going to topcoat the fastener, zinc-nickel is almost surely a better choice than either zinc or nickel and may be a bit less expensive than nickel and more expensive than zinc..
Regards,
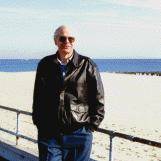
Ted Mooney, P.E.
Striving to live Aloha
finishing.com - Pine Beach, New Jersey
(Ted is available for instant or longterm help)
August 10, 2010
Q. Which plating would be a good alternative to cad plating suspension bolts for a classic car restoration?
The car won't be driven much, just basically need a plating that looks like cad zinc, and will be safe to use.
- Seattle Washington USA
April 18, 2012
A. Hi Mitch.
Zinc plating is probably okay, and is very widely available. But make sure the plater knows that these are suspension bolts (probably high strength that will require hydrogen de-embrittlement baking).
Regards,
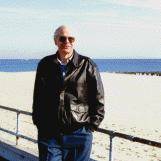
Ted Mooney, P.E.
Striving to live Aloha
finishing.com - Pine Beach, New Jersey
(Ted is available for instant or longterm help)
April 19, 2012
Q. I'm looking for a suitable plating for the steel housing of an E85 compatible fuel pump. High ethanol means the potential for attracting water and the susceptibility to corrosion. The housing is basically tube steel which is crimped at the top and bottom holding the inlet and outlet caps in place. Are either of the plating options in this discussion suitable for this application?
Todd Wilson- Jupiter, Florida, USA
December 17, 2012
Q. I am looking for intelligent opinions on plating hardware of all kind on a Porsche road/race car. This includes engine studs, nuts and bolts vital for engine operation, engine mounting bolts, etc. Also I am replating all fuel hard lines.
I have a selection of zinc platers and one cadmium locally, among others.
I have had cad plated in the past and some decorative nickel.
Please help if you can. It's greatly appreciated.
- Grain Valley, Missouri, USA
April 20, 2013
A. Hi. Even critical jetliner parts are no longer cadmium plated despite its advantages, because of its cumulative toxicity, so cadmium should not even be considered. Nickel is a decorative finish, not intended primarily for underhood components. Zinc plating should be good. A plating of zinc alloy like zinc-cobalt, zinc-iron, zinc-nickel, or my preference tin-zinc should be even better.
Regards,
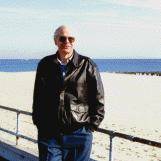
Ted Mooney, P.E.
Striving to live Aloha
finishing.com - Pine Beach, New Jersey
(Ted is available for instant or longterm help)
April 23, 2013
Q. Hi, I read with interest your remarks regarding the options for plating nuts & bolts, etc., now that cadmium plating is no longer available.
I am renovating some old British motorcycles and would like to get the parts plated; and I see there are many kits such as zinc/cad or just zinc but what are the safety issues regarding hydrogen embrittlement?
I understand that load bearing bolts or high stress hardened steel has to be de-embrittled after plating.
I have had my LOTUS front suspension trunion legs done some years ago, is it too late to bake them now or are they likely to fail ?
- Hull, East Yorkshire, England
October 23, 2013
A. Hi Les. Baking for hydrogen relief must be done within hours of the plating. Some say 12 hours is okay, some say much less, especially for the highest strength ones.
But the need for hydrogen de-embrittlement is not a recent discovery or an obscure fact. If they were plated by an established shop who knew what they were, I suspect that the parts for your Lotus were properly baked all those years ago.
Regards,
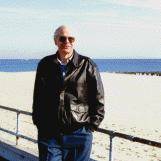
Ted Mooney, P.E.
Striving to live Aloha
finishing.com - Pine Beach, New Jersey
(Ted is available for instant or longterm help)
October 2013
Q. As Cadmium Plating has been banned in India, I want to know which would be the better equivalent? We are basically looking for protection from Corrosion only. Majority of components are not liable for any torque OR pressure. Only few components have threaded parts.
Need suitable alternate ... Is Zinc-Cobalt the better option as compared to simple Zinc plating?
- Indore, Madhya Pradesh, India
October 24, 2014
A. Hi Nilesh. If only corrosion resistance is important, zinc plating is probably fine; most inexpensive hardware is zinc plated. Zinc-cobalt or Zinc-nickel would offer additional corrosion protection at the same thickness for somewhat higher cost. Tin-zinc is more costly because tin costs a lot more than zinc.
But we do have to ask ourselves why, if only corrosion protection is required, cadmium was specified in the first place. It can be dangerous to assume that the people before us were dumber than we are. It's possible, but not a sure thing. Zinc generates bulky, sticky, corrosion products … are we sure that's okay?
Luck & Regards,
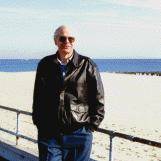
Ted Mooney, P.E.
Striving to live Aloha
finishing.com - Pine Beach, New Jersey
(Ted is available for instant or longterm help)
October 2014
? Dear Nilesh Mahajan
Where is it mentioned that the cadmium plating is banned in india?
- Coimbatore,Tamilnadu, India
October 6, 2015
October 31, 2016
Q. Hi,
I have read numerous posts here and eventually found this thread.
I have been hunting for information and thought you might be able to help.
I have been restoring a motorcycle and I need to zinc plate some nuts and bolts and small parts. During the research of how to do it I realised that perhaps nickel plating is a better option since it looks better and it is more resistant.
Am I correct to the say that about about zinc vs nickel?
Additionally, after reading all these posts by you and others here it seems that it is required to perform hydrogen embrittlement relief or that the parts can break more easily under pressure. Is that a correct statement?
Most of the parts I am going to plate are not going to take any pressure or torque but some nuts and bolts will. For example the bolts that hold the wheels.
Last but not least, are you able to recommend a DIY method for me to plate these parts at home?
Thanks in advance.
Vini
- Sydney, Australia
A. Hi Vini. Nickel plating is certainly not "better" than zinc plating although there may be a few cases where it's more appropriate; yes it is shinier. Hydrogen embrittlement relief baking is required for all high strength components, but not for mild low carbon steel components.
If you want to play around with plating as a hobby, you could start with our FAQ, "How Plating Works", and gradually start learning. But for an amateur with no experience, no baking oven, and no notch testing equipment, it would be a mistake to try to plate high strength fasteners. Good luck.
Regards,
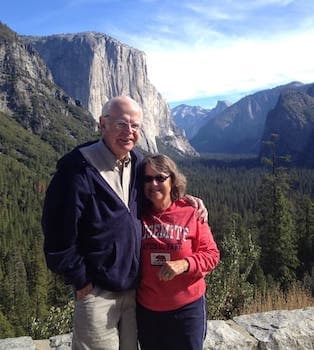
Ted Mooney, P.E. RET
Striving to live Aloha
finishing.com - Pine Beach, New Jersey
(Ted is available for instant or longterm help)
November 2016
Is nickel or cadmium better in water based adhesive
Q. A customer is asking us to produce nickel or Cadmium flakes into their water based adhesive. We are wondering which substrate will remain or will/could become anodic?
Thanks for your help,
Brent
R&D - Salt Lake City, Utah, USA
November 10, 2016
A. Hi Brent. Unless you know something really important about the application that you haven't told us yet, don't even dream of adding cadmium flakes! Cadmium is a biocumulative toxin that the world has been struggling mightily to get out of the environment.
Because you are mixing the flakes into an adhesive, you are apparently calling the flake material "the substrate", but that is the opposite sense to the way finishers use the word "substrate", so it could become a source of confusion :-)
To us, the substrate is the material you are applying the adhesive onto. Whether a metal is anodic or cathodic must be said with regard to another metal. Nickel flakes will be cathodic to a steel substrate; cadmium flakes will be anodic to a steel substrate. Other common metals which are anodic to steel are zinc and aluminum, which sound like much better choices than cadmium.
But just so we don't mislead other readers, we should mention that zinc and/or aluminum flakes are commercially mixed with oil based or water based solvents and available as products like "cold galvanizing" spray paint, and "zinc-rich dip-spin coatings". Good luck.
Regards,
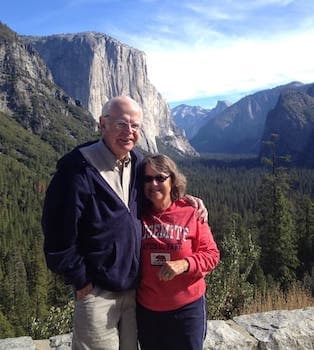
Ted Mooney, P.E. RET
Striving to live Aloha
finishing.com - Pine Beach, New Jersey
(Ted is available for instant or longterm help)
November 2016
March 1, 2017
Q. Hi Ted,
Many thanks for this informative site, and congratulations on keeping it relevant for such a long time.
My question is this:
I want to plate a couple of small sheet metal parts - a mild steel timing cover on an engine, the mild steel rocker covers and a mild steel cover plate on the back of the differential.
Corrosion is not a major issue, but I need to get a smooth, clean and shiny surface because I want to do a translucent 'black chrome' finish on the surface. The cleaner and shinier the surface, the better the 'black chrome' finish will look, apparently.
Can I do a zinc coating then follow on with a nickel coating to get a really solid and shiny surface, or would a straight zinc coating polish up enough.
Best regards
Pete B
Amateur car restorer - Victoria, Australia
A. Hi Peter. I'm not sure that plating them at all is a good idea since the base coat of your "black chrome look" paint may not adhere properly to zinc or nickel. I think buffing the steel would be a better idea.
Regards,
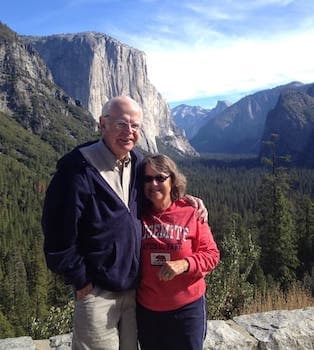
Ted Mooney, P.E. RET
Striving to live Aloha
finishing.com - Pine Beach, New Jersey
(Ted is available for instant or longterm help)
June 2017
Q. What is a good plating to adhere to porosity filled pores with an alum based epoxy that has been machined. we need a nickel based plating over the product caliper pistons. I'm thinking electroless nickel? Any help
Jose delgadocardone industries - brownsville, texas, USA
August 6, 2018
A. Hi Jose. I rather doubt that any plating will prove satisfactory for 'porosity filled pores'. Please look into 'vacuum impregnation' before the plating.
Regards,
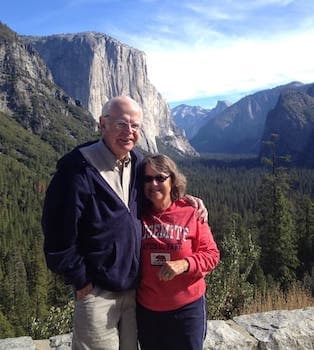
Ted Mooney, P.E. RET
Striving to live Aloha
finishing.com - Pine Beach, New Jersey
(Ted is available for instant or longterm help)
August 9, 2018
A. Vacuum impregnation is a good idea. An anaerobic sealant may also work.
Lyle Kirmanconsultant - Cleveland Heights, Ohio
August 2018
October 24, 2018
Q. Hi Readers,
I appreciate any advice you can give. Apologies in advance for the long question.
I have a large alloy steel bolt made from SA-193 B7 (AISI 4140, 35Rc or 105 ksi tensile) that gets installed into a structure and potentially left for up to 40 years. Currently, we use a Xylan coating which is not holding up to the environment this bolt is subject to, and we've had trouble removing some bolts for inspection after only 3 years in service. Therefore, we are actively searching for a replacement.
The requirements for this plating are as follows:
- Corrosion resistance is critical; bolt is often installed in a coastal environment, and when bolts get wet, they can stay wet for a prolonged period.
- Significant wear resistance not required, bolts are rarely disassembled, but must be able to be disassembled at any time.
- Bolts are hand-tightened, not under a significant amount of tension.
- Cannot use anything containing Cobalt under any circumstances. Cannot rely on Teflon, as it degrades rapidly in this specific environment.
- RoHS compliance not a concern. Cadmium okay, Hex Chromate okay. Coating performance is the priority.
- Must be able to survive constant elevated temps of up to 250 °F.
- Due to thread requirements, must not have an excessively thick build-up (i.e., no hot-dip galvanize).
- Bolt threads will be coated with a nickel-based anti-seize prior to installation.
Our process currently approves a "Cadmium plate or similar" coating or plating for the bolt in question, but I don't believe we've ever actually ordered Cadmium. I've contacted two well-respected platers, and they've both recommended the same 2 finishes:
1) First Choice: Alkaline Zinc-Nickel with Tri/Hex Chromate
-or-
2) Second Choice: Electroless Nickel (High Phos.)
After doing research, I have some concerns with both of these options. The Zinc-Nickel has corrosion protection similar to the Cadmium, but lacks the lubricity of the Cadmium plate, especially when corroded. It tolerates the neutral salt spray test better than the Cadmium, but I'm not 100% sure that will translate to real-world corrosion protection. I'm also concerned about the 'gumminess' of the Zinc-Nickel corrosion products relative to the Cadmium. Per Boeing, the breakaway torque of Zinc-Nickel after 500 & 1000 hours of salt spray test is significantly higher than that of Cadmium. Being able to remove these bolts is critical, and avoiding red rust at the expense of having the bolt frozen by white rust doesn't help in the long run. I've found multiple technical papers from Boeing, Raytheon, and at least one academic thesis that question the suitability of Zinc-Nickel in replacing Cadmium specifically on threaded fasteners.
The electroless nickel has many of the properties we would like upon initial examination, but because it isn't a sacrificial coating, any damage would allow the corrosion of the steel to begin. These bolts are heavy, each weighs over 30 lbs, and it wouldn't take much to damage the surface and cause problems during removal.
So, the current options I am considering:
1) Stick with the Cadmium and spec the bolt with a thick Cadmium plate, Class 12, Type II per ASTM B766
2) Spec an EN underplate and plate with a slightly thinner Cadmium plate, Class 8, Type II per ASTM B766
3) Investigate the Zinc-Aluminum dip-spin coatings normally used on ASTM A490M bolts (Magnicoat, etc), but I'm not sure if they will work with a part of this size & weight due to the difficulty of spinning.
4) Spec the Zinc-Nickel Plate with hex chromate per ASTM B841 and hope for the best.
I'm leaning towards option 2 as theoretically it should be the best of both worlds, but if anyone has any advice or suggestions, it would be greatly appreciated. Thank you.
- Philadelphia, Pennsylvania USA
A. Hi Andrew. Although I am not personally familiar with plating cadmium on top of electroless nickel, thread 44575 talks about it, from which I infer that it's doable and practical. And I see nothing in your description that seems to contra-indicate it.
While cadmium and hexavalent chromate conversion coating are undesirable environmentally, no alternatives offer anything approaching their successful application history as a robust solution ... including against the unanticipated. I think your solution 2 sounds very good. Best of luck.
Regards,
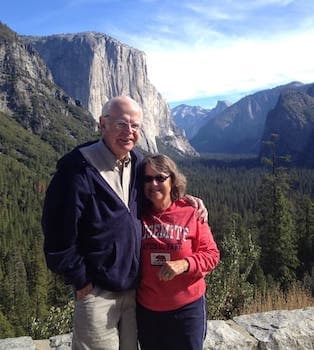
Ted Mooney, P.E. RET
Striving to live Aloha
finishing.com - Pine Beach, New Jersey
(Ted is available for instant or longterm help)
October 2018
Q. Hi there, I just have a quick question.
One of our customers has just specified a harness connector as Electroless nickel plated to connect to an Olive drab Cadmium plated one. Is this likely to cause any corrosion problems?
Aerospace cable harnesses - Truro, Cornwall, England
June 5, 2019
A. Cadmium and electroless nickel, and most other nickel platings will most definitely cause galvanic corrosion. For most applications the standard galvanic potential charts on google can be used and the difference between nickel (ignoring the phos) and cadmium will be great enough to cause a cell. In most expected cases the cadmium will corrode as it is less noble. Of cause what you see on the parts may be variable on the chromate coating that's on the cadmium part, but I don't have enough information to comment on that.
If this test is for a lifetime of a part anyways. The current shift is towards zinc based products as zinc is sacrificial to cad, can be chromated and is cheap.
- New York USA
June 26, 2019
I'm in a situation where I'm attempting to identify some old parts of unknown composition. They should all be nickel, zinc, or cadmium plated steel. Outside of any type of lab environment, is there an easy way to determine the plating? These are mostly thin plated sheet steel parts, probably 50 - 80 years old, showing various levels of corrosion, though none in bad condition. Thanks for any advice you may have.
Doug SkinnerGeneral Contractor - Pilot, Virginia, USA
June 24, 2019
A. Hi Doug. Judging solely from appearance is never sure, but if the parts are strongly yellow (more or less brass tone), they're not nickel, they're zinc or cadmium with a yellow conversion coating. If they are dotted with tiny pits of rust on them, looking something like volcanos when viewed with a magnifying glass, it indicates that the base metal is being anodically sacrificed to the plating instead of the other way around, and the plating is probably nickel or nickel-chrome. How do you know they're not tin, or terne though?
There are chemical spot tests that could be tried, or a local scrap yard may have an instrument for this.
Regards,
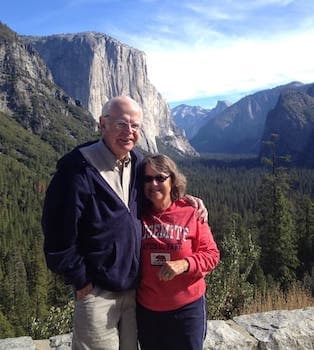
Ted Mooney, P.E. RET
Striving to live Aloha
finishing.com - Pine Beach, New Jersey
(Ted is available for instant or longterm help)
October 2019
Q. I'm currently dealing with a large Cadmium Plated part for the Aviation industry; It's approximately 12.500" Round in Diameter, and 90" Length, It has a thread on the OD roughly 72" in length, We need corrosion protection as well as lubricity on the thread. After reading many of the questions and responses, doesn't look like there would be much better than the cad plating unless someone has a better suggestion to bring before the engineering department for consideration. If that's the case could someone perhaps point me in the correct direction for suppliers of Cad plating in the Ohio or surrounding area.
Thank You
Scot Industries - Wooster, Ohio, USA
August 22, 2019
Ed. note: This RFQ is outdated, but technical replies are welcome, and readers are encouraged to post their own RFQs. But no public commercial suggestions please ( huh? why?).
A. Hi Robert. You're probably right that cadmium is the ideal coating for your application; it often is -- because nothing can match it's combination of lubricity, corrosion resistance, freedom from gummy corrosion products, compatibility with aluminum, and other properties.
Although cadmium is toxic and bio-accumulative, I personally find it ridiculous & tragic that we're spending years and fortunes trying to remove it from critical aerospace components where it has proven itself for decades, while every few years we have yet another instance of it being found in children's jewelry and that being considered no big deal, just a routine recall to try to catch the bulk of it. Even still, there are those who feel it must be eliminated, so you may be pursuing a dead end in specifying it for a new part.
When looking for an alternative -- and I think you realize this -- nothing offers ALL of the properties of cadmium; instead, you have to decide which of its properties are essential for your application and which are unimportant or of lower importance.
We cannot publicly suggest shops except for our supporting advertisers, but potential vendors can contact you.
Regards,
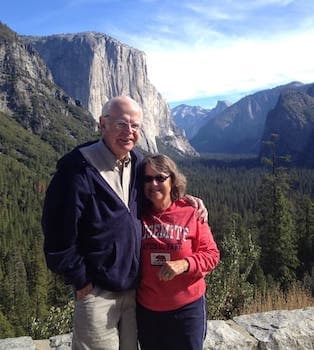
Ted Mooney, P.E. RET
Striving to live Aloha
finishing.com - Pine Beach, New Jersey
(Ted is available for instant or longterm help)
August 2019
A. Robert Galinski:
While there is concern about cadmium toxicity, it is still fairly widely available.
We aren't supposed to recommend specific businesses, but if you will look around Ohio...
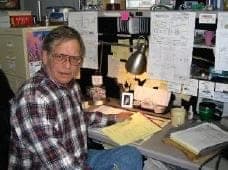
Jeffrey Holmes, CEF
Spartanburg, South Carolina
August 22, 2019
A. I have heard that Zinc Nickel is being looked at as a replacement for Cad, as well as IVD aluminum; neither are as lubricious as Cad, but do seem to offer better corrosion protection.
Alan West- Patuxent River, Maryland, USA
October 30, 2019
Q, A, or Comment on THIS thread -or- Start a NEW Thread