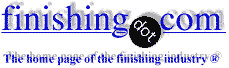
-----
Iron Phosphate Coating Process
Q. We manufacture steel and aluminum panels for testing paints and coatings. We also supply panels pre-treated with Iron Phosphate. The chemical used is Bonderite 1000, with a chrome seal.
A customer has raised concerns that the performance of the phosphate coating deteriorates over time (if stored for long periods prior to painting). They also claim that baking the phosphate coating prior to painting improves performance.
Is there any reason baking prior to painting would improve performance and what is the reason for the deterioration in performance over time of an unpainted phosphate coating?
Patrick PattonWestlake, Ohio
2001
A. Hi Patrick,
It is true. Phosphate coatings have high specific surface area. Phosphate coatings tend to absorb water and other organic compounds from atmospheric environments in terms of capillary effect with time, particularly in the humid areas and industrial fields. Both water and other organic contaminants are harmful to paint adhesion. Baking at an adequate temperature is able to eliminate water and the organic contaminants absorbed over time.
Regards,
Ling Hao- Grand Rapids, Michigan
2001
Phosphating - Shelf Life
Q. We are manufacturers of bearing pins which have to be assembled by a press fit method into ball bearings. As these pins are being shipped by sea to our end user we are worried about the phosphate coating developing rust. Can anyone advise on the best method to increase shelf life? Is there any lacquer coat available to enhance life?
Ronald FredericksSuper Engineers - Pune, Maharashtra, India
A. Sir ji,
Apply the drying or non drying rust preventive oil after phosphating it will give you 1000 hours salt spray life. You can get parker dw 36 or parker 20t from Chemetall Oakite .
Regards,
Qutubuddin Saify- Ajman, U.A.E.
A. Absolutely should have a seal. Chrome good, have to treat for chrome rinse water. Non-chrome sealers equivalent to chrome protection just as good. If you are buying proprietary phosphate, that supplier should have a seal.
Bill Hemptech svc. w/ chemical supplier - Grand Rapids, Michigan
Iron Phosphate Treatment Process: more coating weight & more corrosion resistance
Q. I want to know details about iron phosphate treatment for corrosion protection. Specifically, the pre-treatment of a mild steel surface, the phosphate itself (any hazards in handling?) and any necessary post wash treatment. The parts are oily coming to the process and I am washing off the oil with a powder cleaner that makes a very strong solution and can burn my skin. Also, if the parts are not treated with an additional rust inhibitor for storage, they will rust within a week in the shop.
Sally Clark- Columbus, Ohio
A. Hi Sally,
Your question is somewhat lacking in details, but I can try to answer anyway.
I assume that you want a suggestion for a pretreatment operation that utilizes iron phosphating. How many stages does your system contain? Is it spray or immersion?
The best phosphating scenario would be clean in Stage 1 (sounds like you're already doing this), water rinse in Stage 2, iron phosphate in Stage 3, water rinse in Stage 4, post-treatment in Stage 5.
How you set this up depends on the end use of your parts. You say that the parts rust after a short period of storage. This is not unusual because an iron phosphated surface does not have a great deal of corrosion resistance in and of itself. Iron phosphating is a widely used pre-paint treatment. Ideally, you would paint the parts right after applying the phosphate coating. If the parts are not going to be painted, then you can apply some kind of rust inhibitor that can act as a barrier to corrosion.
As far as handling the iron phosphate, these are strong acid products; rubber gloves ⇦ on eBay or Amazon [affil links] and eye protection (goggles ⇦ on eBay or Amazon [affil links] ) are the minimum equipment. Check your chemical supplier's MSDS for details.
George Gorecki- Naperville, Illinois
Q. I need a kind of anti-rust powder when cast iron part is phosphated, it enhances the antirust effect, to form a pattern in black and grey. How to get it? What is the price? Thanks a lot!
John Rivermachining - Hanzo, Zejon, China
2004
A. Sorry, John, I don't understand the question. Are you suggesting that the phosphatizing that you are presently providing is not corrosion resistant on cast iron, but you have seen phosphatizing done that was corrosion resistant, and you are wondering what chemical you saw someone add to their tank to adjust theirs and tailor it to cast iron?
Two possible solutions are:
- to order a phosphatizing process from a reputable supplier, which will include technical data sheets (you will find a number of suppliers listed in our directory of Chemicals and Consumables, or
- to study phosphatizing in more detail from one of the books previously mentioned. Best of luck.
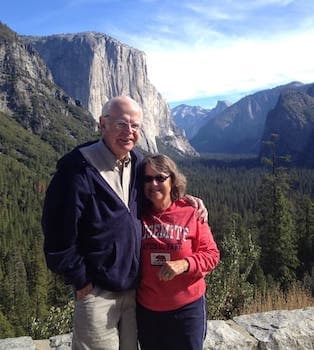
Ted Mooney, P.E. RET
Striving to live Aloha
finishing.com - Pine Beach, New Jersey
2004
Q. I want to know whether it is possible to increase the iron phosphate coating weight to Minimum 0.6 gm/sq.m. for better corrosion protection by means of increasing concentration, trying different additives, accelerators or any speciality chemicals?
Nilesh BaraskarEmployee - Mumbai, Maharashtra, India
2005
A. Hi Nilesh,
You can increase coating weight by increasing contact time, temperature and concentration. But increasing the coating weight will not necessarily improve corrosion protection. Corrosion resistance is related to the composition of the coating, and not the amount.
- Naperville, Illinois
2005
A. Dear Nilesh Baraskar,
If corrosion resistance is your only concern then try zinc phosphating.
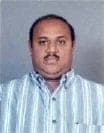
T.S.N. Sankara Narayanan
- Chennai, Tamilnadu, India
(ed.note: The good doctor offers a fascinating blog, "Advancement in Science" )
2005
One-step phosphating
Q. I want to make a solution for degreasing and phosphating in one step (spraying). Can you help me?
Thank you.
chemist - cairo egypt
April 27, 2009
A. Hi, James. That would be an "iron phosphating solution". Although the best of these are patented or trade secret, yes, you can formulate your own. Please try to get hold of a few expired patents on the iron phosphating processes (it's so easy today), and also look into the principles behind the process in Preparation of Metal for Painting ⇦[this on Amazon affil links] or "Phosphating of Metals" ⇦[this on Amazon or AbeBooks affil links] by Werner Rausch.
Just remember that oils & soils are best removed in hot alkalies, so it's not ideal to try to remove them with the cooler, acidic iron phosphatizing solution; and an iron phosphatizing solution won't work its best when oils & soils are floating around in it. You can toss the apple pie into the chicken soup to save a bowl and a step, but no matter how well you do it, it's just not going to work as well as keeping the soup and the desert separate. Good luck.
Regards,
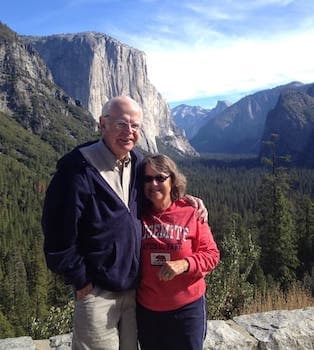
Ted Mooney, P.E. RET
Striving to live Aloha
finishing.com - Pine Beach, New Jersey
April 28, 2009
Q. Our surface is metal for interior of car bodies.
I need to reinforce passivation in pretreatment line. I use iron phosphating. I use Cr6 for passivation but I need to increase corrosion resistance.
Some of my friends say if I use TETA (Triethylenetetramine) in Cr6 tank, it will give better corrosion resistance than before.
- Iran
February 1, 2013
A. Hi, Nader. I feel you should be eliminating Cr6 passivation, because of its toxicity, rather than trying to reinforce it. I'm not familiar with TETA as an additive to Cr6 passivation, but I think you probably need to improve the iron phosphating itself or move to zinc phosphating rather than look for a magic final rinse additive to fix it. Good luck.
Regards,
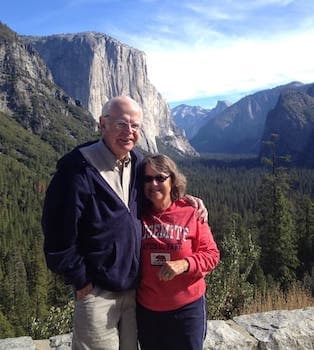
Ted Mooney, P.E. RET
Striving to live Aloha
finishing.com - Pine Beach, New Jersey
March 7, 2013
Q. Hi
We are doing a WBC grade cast iron parts Hot Zinc phosphating (7 tank Process) and then powder coating.60% of the surface is covered with powder coating and remaining as phosphating finish. Our customer doesn't want to apply rust preventive oil on the phosphated surface but requires to have good shelf life against rust before assembly.It is being shipped to different countries by sea/Air, takes 1-2 months. My question is
How long (hrs or days)the good Zinc phosphated parts (having 4.5 g/sqm coating weight) will withstand against rust in general atmospheric condition?
Thanks
Srini
- Bangalore, India
February 15, 2013
A. Hi Srini,
A zinc phosphated surface with no supplementary treatment is going to have a very short life before corrosion starts.
I don't know how easy this would be for you to do, but you could consider vacuum bagging parts, so removing the air that would cause the problem, or maybe you could bag and inert gas charge the bags (e.g., nitrogen or argon). These methods will stop the onset of corrosion.
Aerospace - Yeovil, Somerset, UK
February 18, 2013
Q. Iron Phosphate treatment was meant to increase adhesion of paint for steel drum.
Chinese and Japanese industrial packaging manufacturers use iron phosphate to increase drum's interior cleanliness.
I heard this might be shorten the shelf life of steel product, because the oil residual washed away. What's the pros and cons you think of this treatment?
Industrial packaging steel drums - Shanghai, China
March 15, 2013
Q, A, or Comment on THIS thread -or- Start a NEW Thread