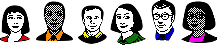
Metal finishing Q&As since 1989
-----
Electro versus electroless nickel
I am the quality control manager for a fastener manufacturer. We cold head a ball stud that is used as a pivot for a windshield wiper motor. This part is electroless nickel plated after it is manufactured. Recently we received parts from our plater that are considerably duller in appearance than what we are used to. This concerns our customer as the appearance has suddenly changed (not necessarily bad but different). Our plater claims nothing has changed in their process but it is obvious that something has changed. Does anyone have any information that may be helpful?
I have also been asked by our customer to compare the benefits of electro nickel versus electroless nickel. As the nickel is deposited for protection against wear any information about the wear characteristics as well as appearance would be helpful.
Jim Wolters- Grand Rapids Michigan USA
Electroless nickel is significantly more expensive than electroplated nickel, but it is better in several respects. Basically it is like a "glass" due to its high phosphorus content and is less porous and more corrosion resistant, while also being much harder and more wear resistant.
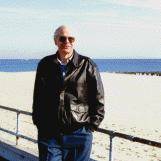
Ted Mooney, P.E.
Striving to live Aloha
finishing.com - Pine Beach, New Jersey
Jim:
Your supplier's bath is probably a medium phos commercial bath and it's out of balance or getting old (too many turnovers) hence is loosing its ability to produce bright deposits. Point to him that you want a bright deposit. He can fix it by adjusting his chemistry or preparing a new bath. Regarding the change of EN to electronickel, I personally don't think is correct. It's hardness, lubricity and thickness uniformity are considerably lower. You will lose durability and precision.
Guillermo MarrufoMonterrey, NL, Mexico
I agree with the post from Guillermo and would suggest that your work is plated in a bath with less than 4 metal turnovers. In a bright electroless nickel bath, over time the brightness will decrease but the engineering characteristics will not change. Electrolytic nickel will not produce a uniform deposit and the threads of your fastener will have a much higher thickness than the middle of the fastener.
Mark C. Reppa- Plymouth, Michigan
Mr. Jim,
I agree with all the others and would like to add that if the most important property required for your pieces is wear resistance as well as hardness and uniform deposition, go on with the electroless nickel. You can also achieve much higher hardness (up to 1000HV) with the proper post-heat treatment of the piece, but with a loss of corrosion resistance.
What about the surface condition and appearance of the parts from you, before the nickel plating? I assume that it hasn't changed since you say it is the plater's fault.
Ask your plater how often he analyzes and corrects the Ni concentration of his bath. The chemical analysis is very simple as well as keeping all the parameters right (pH, temperature).
Christos Sigalas- Athens, Greece
If your main goal is wear resistance you should ask your plater for a low phosphorous EN.
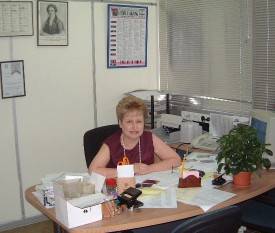

Sara Michaeli
Tel-Aviv-Yafo, Israel
Q, A, or Comment on THIS thread -or- Start a NEW Thread