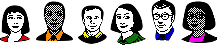
Metal finishing Q&As since 1989
-----
How many hours salt spray equals 30 years life?
Q. I need information about how much exposure time in hours, to make salt spray test with zinc coated cable for use in overhead lines structures for a expected period of life about 30 years.
Dante Sagula FilhoLautec Empreend. Com. Ltda. - Sao Paulo, SP - Brasil
2000
A. First of all, you should know that nobody can directly correlate salt spray hours to real service life. Specifications for a fixed number of salt spray hours exist, and these specifications do have a years-of-service target, but there is no definitive correlation between salt spray hours to years of life.
I would say that for 30 years of service, your cable should be able to last at least 2000 hours of salt spray before the first sign of red rust. I do not think a plain coating of zinc can give this sort of performance. You may be able to get this from a good zinc-alloy plating with a big, thick, hex chrome passivate, possibly with an additional post-treatment.
30 years is a very long time for most electroplating and hot-dip processes. You need something with high-quality performance. I work in the automotive industry which targets 10 years, and plain zinc is usually not good enough for us.
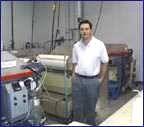
Tim Neveau
Rochester Hills, Michigan
Multiple threads merged: please forgive chronology errors :-)
Q. I am a student in electromechanical engineering and I am doing my thesis about corrosion and especially about corrosion-tests. I have to make a matrix of different ferro-metals with common coatings involving how long these materials, combinations of both are resistant to corrosion. The main goal is to link corrosion-tests with reality.
For example: five years in a marine environment is the same as ? hours in a test chamber. My question is: is this done before? What is the best way to start with this? Which tests are most used to do this kind of research? Prof. Bogaerts of the University of Louvain told me that test results of ferro-metals with certain coatings, and their life expectation in a corrosive environment, exist in literature. He just doesn't know where to find them.
Could you help me out?
Matias Kerkhofs- Louvain, Belgium
2001
A. I am afraid your endeavors are doomed for failure! There have been many attempts to directly correlate corrosion testing to real life exposure, but no such correlation exists between a laboratory test method and real life. This is especially true for the most common corrosion test method, salt spray via ASTM ASTM B117.
The main problem is that a reaction that takes one month is occurring via a different mechanism than one that takes 15 years. In general, the more you accelerate corrosion, the lower relevance it has on real life.
Industrial practice is to specify a number of hours of salt spray the part should last to white corrosion and/or red rust. Sometimes it is to the first sign, and sometimes until a certain percentage of the significant surface is corroded. More hours for parts that will see harsher environments. Corrosion testing is used for quality-control to pick out bad parts, and to compare different finishes. Predicting the life of a finish is generally made from real life observations and experience.
I work in the automotive industry, and GM, Chrysler, and Ford have developed durability tests that involve 6 months through a harsh daily schedule of exposure at a large proving ground facility. They claim these tests do correlate to real life exposure. However, these are not laboratory methods. I'm also a bit skeptical about how well these tests really correlate to real life.
If you want to know how long a certain finish should last, call a plater or plating chemical supplier and ask. There are a huge number of finishes and many variances on how they are applied. A full list does not exist, and you will need to compile it for the finishes you are interested in.
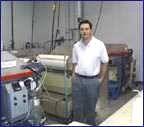
Tim Neveau
Rochester Hills, Michigan
- Leuven, Belgium
A. Sounds to me like it works through precision without accuracy :-)
There is no relationship between spray hours and real life because the corrosion mechanisms are fundamentally different, with the result that some finishes that outperform others in the test cabinet cannot actually match them in real life.
So a correlation coefficient can, at most, apply only to a specific coating on a specific substrate, not coatings in general.
Many finishes outlast galvanizing in a salt spray cabinet whereas there is no other finish which even comes close in real life -- 50, 75, sometimes even 100 years and more with no maintenance; there is a reason why electrical transmission towers are always hot dip galvanized :-)
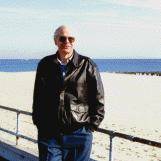
Ted Mooney, P.E.
Striving to live Aloha
finishing.com - Pine Beach, New Jersey
Multiple threads merged: please forgive chronology errors :-)
Q. We are doing some salt spray testing on aluminum fishing reels. Does anyone know of a correlation between salt spray hours and real life service?
Vic Waldman- Naugatuck, Connecticut
2002
A. Hi, Vic. A well anodized surface will last longer in a salt spray cabinet, and in the real world, than a poorly anodized surface. Unfortunately that's the end of the correlation :-)
The corrosion mechanism is different and the reactions are different. For example, in the real world galvanized coatings build zinc carbonate reaction products by slowly reacting over time with the carbon dioxide in the air. These adherent and resistant corrosion products help galvanizing last for 50 to 60 years severe exposure in the real world; other coatings can't touch it. But in a salt spray cabinet where the carbonates have no opportunity to form, galvanized coatings perform poorly.
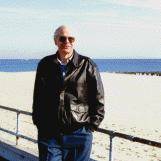
Ted Mooney, P.E.
Striving to live Aloha
finishing.com - Pine Beach, New Jersey
A. Hi Vic,
No correlation exists between salt spray performance and real-life service.
George Gorecki- Naperville, Illinois
A. I have always said that salt fog testing is too widely used and abused. I say this because, the environment within the salt fog chamber is salt. Unless your product will see real world environments such as the salt chamber, there would not be any correlation. Further, aluminum generally is not put into a salt fog chamber, because it would take a very long time to destroy the integrity of the topcoat on an aluminum surface. I believe that many times, companies do not use powders thats may have failed in the salt fog arena, but certainly would pass many more hours of regular moisture. A better idea would be to ask your test experts to use a cyclic chamber instead of the typical salt fog chamber. I believe the cyclic chambers will become more prevalent in the future for this very reason.
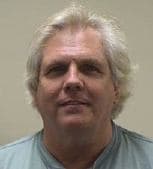
Bob Utech
Benson, Minnesota
Q, A, or Comment on THIS thread -or- Start a NEW Thread