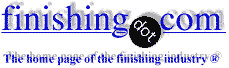
-----
How to do copper plating
1995
Q. I'm an absolute beginner in electroplating. I would like to copper some iron pieces (plate, pipe); so I've turned or filed to the desired dimension and shape. I've prepared a solution of
copper sulphate
⇦ on
eBay or
Amazon [affil link] CuSO4 (~200 g/l) and H2SO4 (~5 g/l) in water (deionized). When I've used this solution with a copper wire as anode and with 10 mA/cm2 as maximum, the result was very bad. A lot of copper has deposited on iron but rinsing it under water-tap the copper goes away. So I've reduced current density also to zero: if I put iron in the same solution the result is the same: a lot of copper badly attached on iron, and under the copper the iron was oxidized (dark color).
Further attempts (current density between 0 and 100 mA/cm2; no H2SO4 or more than 10 g/l; CuSO4 from 50 g/l to 200 g/l) have produced the same result: I've also tried various polishing by inorganic (HCl, H2SO4, NaOH) and organic (tetrachloroethylene, turpentine, acetone) solvents. Temperature of bath has always been around 18 °C. Only if I put iron pieces in the bath for few seconds and then rinse it, I can get a very very thin copper deposit (I was not able to measure it with .01 mm caliper) that's well attached to iron, but it's so thin that it isn't useful at all.
Where am I wrong? Many thanks in advance.
A. Hello, Lapo. If you (or a reader) wish to demo copper plating for a school science project, we have an FAQ: How Electroplating Works, that will give you easy instructions for the project.
But sorry, your approach won't work for functional electroplating applications because copper is more "noble" than iron and will (as you saw) deposit on steel or cast iron without any current applied. This is called an "immersion deposit" and it usually has virtually no adhesion. Still, make sure that your component is absolutely clean (waterbreak-free) and that current is applied to the part before & while it goes into the plating tank ("hot entry") because that will help a little towards discouraging immersion plating.
The preplate cleaning should consist of caustic cleaning (detergent and NaOH) followed by an acid dip (HCl). But for onesy-twosy work you can scrub the part with a tampico brush and powdered pumice
⇦ on
eBay or
Amazon [affil link] as an alternate to caustic cleaning, and use a diluted HCl for activation.
For functional copper plating on steel you need to either electroplate an initial layer from a nickel strike bath, or from a copper cyanide (very dangerous poison) bath before you will be able to use the copper sulphate bath; these will not immersion deposit. You probably will be best off with proprietary additives (brighteners) to get good, bright, plating.
Electroplating involves working with hazardous chemicals, so it may not be an ideal casual hobby. If your desire is simply to get copper plating on the parts, as opposed to doing copper plating as a hobby and learning experience, plating is a jobshop industry and there should be a commercial plating shop available in your area. Good luck!
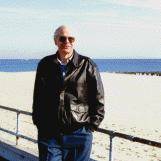
Ted Mooney, P.E.
Striving to live Aloha
(Ted can offer longterm or instant help)
finishing.com - Pine Beach, New Jersey
1997
A. It is not something you would let children do without supervision, and some people might not find it impressive, but I did find a way to plate coins with copper metal. If you insist on trying to plate outside of an industrial environment, at least you won't be using concentrated acids, metal salts, and etc.
I tried to find a way to do this using only nontoxic chemicals (aside from the copper itself), but I needed to use some ethylene glycol. This stuff is toxic, has a sweet taste (or so I am told), and pets and children might be tempted to taste it, so it must be handled by adults and stored in locked cabinets. On the other hand, anything containing copper is not good to drink, and there is enough salt in this solution to act as an emetic.
All of these tests should be done under adult supervision, and the learning experience is bound to be better this way. Depending on the age of the witnesses, you can cover all sorts of exciting things, from cleaning coins with toothpaste to chemical calculations of normality and concentration to electrochemical equivalents. Except for the brightening agent, all other supplies are household items. The ethylene glycol should be stored in childproof areas, and the test solution should be dumped at the end of any experiment. All containers should be labeled, even as you are using them, as a matter of normal laboratory practice.
The solution described is low in the concentration of copper, as far as plating solutions go. If all of my electrolysis converted my copper anode to copper ions, and all of it ended up in the sewer we are talking about:
e =i x r
1.5 =i x 15 ohms
i x 15 = 1.5
i = 0.1 amps
If you run the cell for 2 hours, that's 0.2 ampere hours. Looking up cupric ion, we see that we deposit/dissolve 1.19 grams of copper metal per ampere hour. So the most we could dump down the drain is 0.24 grams, not an ecological nightmare. The final concentration of the cell of 100 cc, after 1 hour of electrolysis, could reach 2.4 grams/liter (this is unlikely, as gassing is very evident, indicating that we are not operating at 100% efficiency).
- 1. Strip the insulation from about 2 feet of copper wire. Clean with toothpaste, Multiscrub, etc. and a sponge or a soft bristle brush. Wear rubber rubber glovesrubber gloves ⇦ on eBay or Amazon [affil link] so you don't recontaminate the wire with oil from your fingers. Coil this up except for a few inches and place in a 150 cc [beakers on eBay or Amazon [affil link] .
- 2. Add 100 cc of white vinegar ⇦in bulk on eBay or Amazon [affil link] , and 1 heaping teaspoon of Kosher salt, and 3-6 cc of ethylene glycol (depending on if it has been diluted).
- 3. Use a nickel, dime or quarter for a cathode. The shinier the surface; the brighter the resulting deposit. Clean as for the copper wire in (1) above.
- 4. Rig a 1.5 volt battery with a 30 to 200 (approximate) ohm resistor in series. Attach the positive terminal to the anode (the copper wire), and the negative terminal to the cathode (the coin).
- 5. Electrolyze this solution for 10 minutes or so. It seems to take a few minutes for some of the copper metal to dissolve and be available for plating. After this you can try plating some new coins. Clean the coins beforehand using an old toothbrush and some toothpaste, rinsing the coins with water (Wear gloves). You will have to look around for alligator clips or locking forceps to make some reasonable connection.
- 6. A copper color should develop after a few seconds of plating. Jiggle the cathode during plating. The plating brightness seems to improve after the bath has been electrolyzed for 20 - 30 minutes.
- 7. You can also plate pieces for longer periods. the deposit turns black during plating of more than a few seconds, but you can polish this deposit to an antique copper finish using toothpaste. The plating is attractive, but you can imagine that it is not as impressive or immediate in visual impact as plating gold onto nickel.
- 8. I had excellent success with adhesion on coins; all of my coins are now copper colored, and I suppose I will have to use them in automatic vending machines unless I want to explain what happened to them. I can't remove the copper with vigorous scrubbing. Just another reason why this process should not be left to children, unless you want all of your conductive trinkets in antique copper. (You DIDN'T let the children plate the tennis bracelet Aunt Constance left me … did you?)
- 9. This solution will copper (verb) iron nails by immersion. The smoother and shinier the iron, the better the copper immersion deposit.
I did not get good adhesion when I tried to electroplate an iron nail; you would need a strike solution, and this would be difficult to make from household chemicals. - 10. Immediately after testing, dump contents into the drain, and wash all equipment with water and detergent, then rinse with tap water.
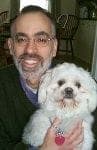

Tom Pullizzi
Falls Township, Pennsylvania
by Steve Spangler
or AbeBooks
or eBay
or Amazon
(affil link)
Hello, Where can I buy some ethylene glycol? Where can I get chemistry equipment in general? I have been searching the net but can only find industrial sites. I don't really need 1 MT of CuSO4!
Great site by the way. Kudos!. Am I correct in assuming that the above formulae for copper plating doesn't require CuSO4?
Thanks for your help.
- New York
Thanks for the kind words, Eamon. I believe that standard automotive anti-freeze is basically ethylene glycol, although it contains some corrosion inhibitors, but check the label. Yes, you are correct that Tom has described a plating process that does not require copper sulphate.
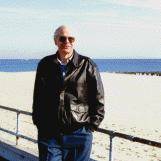
Ted Mooney, P.E.
Striving to live Aloha
(Ted can offer longterm or instant help)
finishing.com - Pine Beach, New Jersey
2000
2000
Suggestions: I tried your household plating experiment and needed to make the following revisions -
ABSTRACT
- 1. Pickle object to be plated in sulfuric (battery) acid, found at auto parts stores or large chain stores.
- 2. Solution Prep
- a. Prepare solution as directed
- b. Use a piece of copper sheet metal
- c. Attach scrap metal to wire connected to negative clip of 12 volt battery charger ⇦ on eBay or Amazon [affil link]
- d. Attach copper to positive terminal
- e. Turn on and shake off solid particles that form after a while
- f. Let the part sit for about a hour and a half - until the solution is bluish when observed from the side
The solution is now ready to use as prescribed by your directions. This formula has been tested 25+ times. Thank you very much.
John MarkgrafMy ol' dad was keen to try and copper plate some leaves but couldn't get the copper to 'stick'.
I sprayed the leaves first with zinc plate (ordinary cold galvanizing compound ⇦ on
eBay or
Amazon [affil link]
aerosol can of for car bodywork) then dunked these in an ice cream tub of copper sulphate
⇦ on
eBay or
Amazon [affil link] with just a tiny drop of H2SO4 (from my car battery) and connected the car battery charger
⇦ on
eBay or
Amazon [affil link]
to a piece of copper pipe (about 8 inches) and the other side to the coated leaf. I did put a small 12 volt bulb in series with it all to limit the current but I ended up with quite a nice copper coated leaf. My old man was highly delighted.
- United Kingdom
2000
I am looking for a reasonably simple process in which I can plate copper metal onto a nonconducting substrate such as Kapton or Mylar (both plastics). Electroless would be preferable, but not necessary. If anyone knows of a particular kit I could purchase that would be even better, although not necessary.
Nikolas Uhlir- Alexandria, Virginia
2000
2001
FOR Nikolas
MIX 1 TO 3, PRE THINNED VARNISH WITH COPPER POWDER, ATTACHING WIRE TO OBJECT AND COATING WIRE END UP INSULATION ABOUT 1/4 INCH. LIGHTLY DUST WITH SAME POWDER. THEN PLATE AS NORMAL (ALLOWING VARNISH TO DRY
12 HOURS.--WORKS FOR ME 1 PART-POWDER/3 PARTS TH.VARNISH).
- PHENIX CITY, Alabama
Now if you're game, try this … it works beautifully. Buy K-77 Root Killer ⇦ on
eBay or
Amazon [affil link]
. Mix one lb. to one gallon distilled water, bath temp approx. 75 degrees. Purchase a paint product from your local dealer of bright copper, metallic spray paint (not the real cheapo). Clean your substrate then spray it good. Allow one hour to dry then plate as usual. Man it comes out salmon pink.
Good luck,
- Phenix City, Alabama
2002
It may be against Federal law to use root killer in a way not in accordance with the indications for use as a root killer. Does anyone know what this stuff is, chemically?
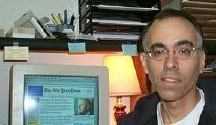

Tom Pullizzi
Falls Township, Pennsylvania
2002
Proprietary products rarely tell you what they are 100%, because then everyone could copy them and claim them to be identical and all their development and marketing efforts wasted, but most root killer is essentially copper sulphate pentahydrate. Yes, there may be some contaminants that could be non-ideal for plating applications. Be beware that some root killers like RootX are NOT copper sulphate.
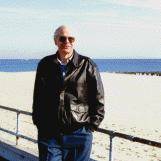
Ted Mooney, P.E.
Striving to live Aloha
(Ted can offer longterm or instant help)
finishing.com - Pine Beach, New Jersey
2002
The composition of K77 root Killer is > 99% Copper sulphate. Here is the Cornell University site for the Material Safety Data Sheet:
http://msds.pdc.cornell.edu/msds/msdsdod/a246/m122546.htm#Section2
- Ottawa, Ontario, Canada
2003
Ed. note: Thanks, Robert. Sorry readers, that domain name no longer works.
Q. I am a 'classic car 'restorer, and one of my biggest headaches is the quality of commercial electroplating work, It is simply not possible, here in the UK, to find any electroplating shop that is willing to spend the required time, and degree of care and understanding necessary when dealing with unique, irreplaceable auto parts.
I have attempted my own dull nickel plating process, with far better end results than any plating shop has ever produced for me, and I would like to try my own duplex chrome plating. This naturally entails an acid copper system (I would use nickel as a strike coat) Proprietary solutions are very expensive compared to commercially available forms of copper sulphate crystals, but I have read, in an item on this website, that there is more to a good acid copper solution than simple copper sulphate and sulfuric acid.
Is this important, given that it is only a 'base coat' for a further two coats of nickel, before the chrome?
Apart from this, is 'agricultural' copper sulphate, i.e., weed killer, too impure to use as the basis for electroplating solution? Any help is greatly appreciated.
Many thanks,
classic auto restoration - Chesham, Buckinghamshire, England
2007
A. Hi, Michael. The purpose of the copper plating (in this case) is to be soft and buffable; most people probably consider "show chrome" to mean highly buffed copper plating under the nickel. But if you are not planning to buff the copper to a mirror shine, I think you'd be better off leaving out the copper plating, and just starting directly with nickel -- that's what most OEMs have done for many years now.
Electroplating shops do not make their copper plating processes from root killer, although they use a great deal of copper sulphate and thus have the potential for saving a lot. If you want to do better work than they, I can't really see using root killer, but only very pure products.
Try to borrow or buy a cheap copy of the Metal Finishing Guidebook or the
Canning Handbook to see the principal differences between professional acid copper plating solutions and root killer, and to what extent they are or aren't important to you in your particular situation.
Good luck!
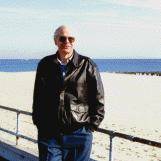
Ted Mooney, P.E.
Striving to live Aloha
(Ted can offer longterm or instant help)
finishing.com - Pine Beach, New Jersey
2007
January 14, 2008
I found this letter while researching copper plating techniques, and I know it's an old thread by now, but it was the first relevant one I saw. In any case, thank you, because it did have the answers to most of my questions.
I do need to say, however, I am a little put off by the attitudes taken by the professionals who have been answering these questions here. Although your first response, Ted, did give a detailed answer to Lapo's question, it ended with and was followed by little more than thinly-veiled dismissal of any inquirers' ability to understand the chemistry behind it and not drink blue vitriol or HCl.
Granted, it is important to warn a complete beginner of the dangers of things like sulfuric acid, but Lapo at the very least showed enough of a grasp of chemistry to understand acids and know how to read MSDS datasheets. And even though Michael Holloway had limited experience with electroplating as well, his knowledge and concern for the importance of the finish on rare car parts is most likely much greater than that of someone who in plating those parts is being paid to repeat the same type of procedures as the last hundred times. It's somewhat similar to why fast food is sloppier and lower quality than its finer restaurant or gourmet counterparts.
And speaking of root killer and MSDS, I did some research and found the datasheet for K-77 Root Killer on the website of the manufacturer, Roebic, here www.roebic.com/pdf/K-77RootKillerMSDS.pdf
It is, in fact, >99% pure Copper(II) sulphate Pentahydrate - the same purity as the LR (low resistivity) grade CuSO4·5H2O that is, according to my further research, commonly used in electroplating applications. Furthermore, I've found nothing anywhere that would indicate that K-77 is any more restricted in legal use than copper sulphate under any other brand, which makes sense - it is no different and includes no other chemicals, and is mostly environmentally safe (disposal via plumbing is ok, dumping in lakes and rivers discouraged but ok in small amounts) except in amounts or concentrations significantly greater than you'll find at Home Depot.
But yes, proprietary solutions do consist of more than copper sulphate and sulfuric acid. they usually also add small (very small) amounts of HCl, because chlorides at 30-100 ppm (depending on the rest of the solution) helps brighten the plating. So does the brightener, usually the main or only proprietary component that I've seen in professional solutions. For an example of the chemical composition of a brightener, check out this patent www.freepatentsonline.com/3715289.html
So, it might be easier just to buy some other company's - in my case anyway, that's where my tinkering with chemistry gives way to my wallet. Expensive, likely. Necessary? The professionals will always tell you yes. It's just my opinion as a casual idiot, but I've seen a few people achieve great results without it.
That's my casual, inexperienced two bits. Likely nobody reads this anyway, but maybe I added something worthwhile.
- Houston, Texas
January 14, 2008
Thanks for your input, Kellin. About 1300 people visit this thread every month, so your contribution will certainly be appreciated!
You could be right that Lapo isn't the beginner he claims to be. But please remember that internet forums are giant one-room schoolhouses, read by 3rd graders and post-doctorates alike, so when someone labels their question as coming from "an absolute beginner", less experienced readers will certainly be expected to be addressed at that level, and need to be warned about things like the hazards of cyanide plating. Dozens of trained professionals have died working with it, including 6 at Bastion Plating in 1984, and a man in my very own town died a few years ago doing cyanide copper plating on his kitchen table, also putting the first-responding police officer in the hospital.
K-77 may well be a root killer that is 99%+ copper sulphate as you say, but you've illustrated the hazard of the procedure perfectly because if others instead select RootX, for example, they get a herbicide with NO copper sulphate.
An "absolute beginner" may not realize that jobshop plating services are readily available, so I advised of that option as well because being "a little put off" can cut both ways:
Many people love boat maintenance, for example, and are happy as a clam spending the day with a beer in one hand and a scraper in the other -- but I'd rather be in a dentist chair. I repeatedly ask on boating sites where I can get so-and-so fixed, only to have people thinking they are doing me a big favor by insisting that I can do it myself instead of answering my question :-)
You may enjoy hobby plating, but others can't stand it, and may appreciate learning that they can get it done rather than having to do it themselves :-)
Ad-hominem postings are distracting, time-consuming, and dilute the useful content of a site -- so please continue to offer advice and contradict any statements you disagree with, but please don't derail the discussion by criticizing myself or other posters. Thanks again.
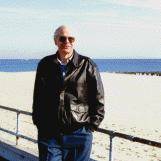
Ted Mooney, P.E.
Striving to live Aloha
(Ted can offer longterm or instant help)
finishing.com - Pine Beach, New Jersey
Q. Specifically doing a sixth grade science project and trying to be the good Dad. Do you think a potato battery will generate enough current to copper plate a small brass key. Can I use copper sulphate dissolved in white vinegar? Amount of copper sulphate to vinegar required? Using a 2 inch piece of copper pipe hammered flat on other wire.
Scott Durham- Charleston South Carolina
January 17, 2008
A. Sorry, but a single potato battery will not suffice, Scott -- although a half-dozen hooked up 3 x 2 or 2 x 3 in series-parallel might!
Any copper sulphate you add will be to the good; it's not critical. So I'd say add enough to give a light to medium blue color. Good luck.
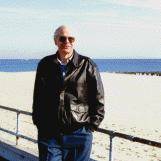
Ted Mooney, P.E.
Striving to live Aloha
(Ted can offer longterm or instant help)
finishing.com - Pine Beach, New Jersey
January 18, 2008
Q. I am a grade nine student trying to perform copper plating with common kitchen products. Mom says nothing too dangerous. My Dad is away, so it's just me and my Mom. We have already used the battery and copper wires in some salt water to see what happens, so I think to take it further would be an interesting project. Every project known to man is already being done. I would love to do something different this year. Thanks to anyone that can help
dalton scottstudent - Canada
February 18, 2008
February 21, 2008
A. See our FAQ on How Electroplating Works for the details for super-safe copper plating for school projects, Dalton -- you can tell your mom that no chemicals except vinegar are used.
As for something different: have you ever decorated easter eggs by writing on the eggs with a white wax crayon or otherwise masking areas before dyeing to keep that area from absorbing dye? Maybe you can clean up a quarter real well, then make symbols with very thin strips of tape or nail polish before copper plating it? Electroplating often involves masking like that.
Best of luck.
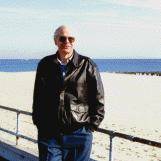
Ted Mooney, P.E.
Striving to live Aloha
(Ted can offer longterm or instant help)
finishing.com - Pine Beach, New Jersey
Q. I have done everything you say from cleaning the surface of the metal & preparing the solution of plating. Everything is good. I wait a time until drying the plating, but when I start to ensure of plating stabilization the plating is not attached & not stabilized on the metal & it goes off & the metal go back to being without plating.
Please I want your help if I have to use stabilizer materials to can make fixation of the plating
thanks,
master study - Isreal - Gaza
October 6, 2008
A. Hi, Khaled. This thread has grown long and rambling, so although you say you've done everything we've talked about, I'm not clear what metal you are trying to apply to what substrate from what kind of solution :-)
But to re-state it from the beginning, you cannot electroplate copper directly onto steel with good adhesion from a copper sulphate solution. Is that what you were trying to do?
Regards,
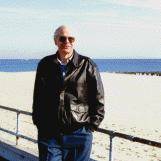
Ted Mooney, P.E.
Striving to live Aloha
(Ted can offer longterm or instant help)
finishing.com - Pine Beach, New Jersey
October 12, 2008
Q. I tried this process as described above, but I can't get adhesion to pewter. It works great on dimes and nickels, but I have some pewter medallions that I want to copper plate and it just gets a black film that wipes off leaving the pewter looking a little greyer than before, but otherwise unchanged. Anyone know what I need to do differently? It is lead-free pewter, but I don't know the actual composition.
By the way … The method does work BEAUTIFULLY on nickels and dimes! Just not pewter.
- Charlestown, Indiana
July 10, 2009
A. Hi, Nathanael. Modern lead-free pewter is 90+% tin, and tin is anodic to copper. That means copper sulphate tends to auto-deposit on pewter as a non-adherent immersion coating just as it auto-deposits on steel. You probably need cyanide copper plating (very dangerous) or a proprietary copper pyrophosphate solution (available from EPI / Electrochemical Products Inc. [a finishing.com supporting advertiser] or Zinex). It is possible that hobby plating vendors offer proprietary copper pyrophosphate plating baths too. Good luck.
Regards,
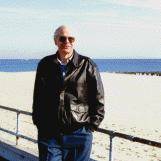
Ted Mooney, P.E.
Striving to live Aloha
(Ted can offer longterm or instant help)
finishing.com - Pine Beach, New Jersey
April 28, 2010
April 28, 2010
To make one liter of solution:
Copper sulphate crystal: 66 grams
Deionized or distilled water: 710 ml
35% Sulfuric acid: 290 ml
35% hydrochloric acid: 0.14 ml
Temperature of solution: 26 °C
Cathode current density: 30 Amps per square foot
Anode to Cathode surface area ratio = 2:1
Voltage: 5 to 12 Volts DC
Use air bubbles or mechanical stirring to agitate solution
- London, U.K.
----
Ed. note: We thank Jonathan, but students and inexperienced hobbyists should know that, with 35% acids, he is no longer talking about the "safe" electroplating some of them were looking for: these are strong acids.
Q. Please explain electroplating of copper. We're doing an experiment where copper is the anode and a metal spoon is the cathode
What effect would temperature have on the appearance of the deposited copper?
What would be the electrodes and the electrolyte?
- Perth, WA, Australia
September 13, 2010
A. Hi, Teresa
The anode and the cathode are the two electrodes. The electrolyte is whatever liquid you put them in. Hopefully you know what temperature is in terms of physical chemistry: it's movement or vibration of the atoms, so higher temperatures are going to aid ion mobility and result in faster electroplating. Whether it's "better" electroplating will depend on a lot of other factors, and I would guess that you are supposed to conduct an experiment to see the result. Good luck.
Regards,
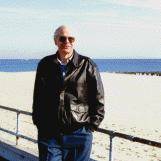
Ted Mooney, P.E.
Striving to live Aloha
(Ted can offer longterm or instant help)
finishing.com - Pine Beach, New Jersey
September , 2010
Q. Okay, so I need a little babysitting on my question /adventure, so please bear with me … I have taken general and organic chemistry in college, I do remember the basic principles, and have always varied a healthy caution, but am a lil rusty ;)
Similar to a gentleman earlier in this thread, I'm trying to copper plate an Auto part, and could really use some technical assistance!
Start with one 20 gallon gas tank that is 60" x 14" x 8", completely covered in rust. I've used the electrolysis to absolutely clean the internal to a beautiful shine, and now am ready to core the steel tank with a material that is far more rust resilient. The idea of being able to copper plate this fuel tank has become the focus of nearly two weeks of evening reading.
Is it possible to plate the tank from the inside out using copper wire, sheet, tube, etc? What type of solution and setup would be most likely to create a good bond between the steel and copper? I noticed on an earlier thread that a high amp charge will cause some carbonation (or darkening) to the surface of the copper. While I do intend to show off my (more or less, your) extremely high intelligence levels, I'm really willing to forego aesthetics for the functionality of the enhanced copper/steel container.
There are 2.5" diameter holes (for the neck where the fuel comes into the tank, and on the other side, a hole that the fuel gauge attaches) on opposite ends of the tank, so I could run a copper tube, wire, etc. through each hole or one at a time whichever would be most effective.
Thanks so much for any and all help!
freight carrier - milwaukie, oregon united states
January 30, 2011
A. Hi, Justin. Gasoline chemistry can be complex and I don't know if copper plating is compatible with gasoline. Plating blind inside a gas tank is exceptionally difficult for an experienced professional; the plating will only go where the electricity goes, and the electricity follows the path of least resistance (the shortest route). so I think you should do quite a bit practice with a less critical item before risking this item that you've worked hard on.
I think if I were you I would test immersion plating from a dilute copper sulphate bath on some similar item and see if you can get enough adhesion. Immersion plating will deposit evenly even in the corners. Put in a fresh fuel filter just in case :-)
Regards,
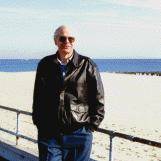
Ted Mooney, P.E.
Striving to live Aloha
(Ted can offer longterm or instant help)
finishing.com - Pine Beach, New Jersey
January 31, 2011
Q. I am curious about vinegar and salt the solution that includes a small amount of ethylene glycol. What does the ethylene glycol do? Is it a brightener? Something else?
Thanks,
Michael
- Bothell, Washington USA
March 8, 2011
A. Hi, Michael.
Something that we keep repeating is that the electroplating experiments we developed are super simple and safe electroplating procedure for elementary school students to demonstrate electroplating for their science projects -- but there was never any intention of it being practical for any actual application at all! Yes, the purpose of ethylene glycol (or better yet, sugar because it is safer), was to play the role of a brightener. Does it really work? Maybe a little bit; the plating is very thin and marginal, so it's hard to tell :-)
Regards,
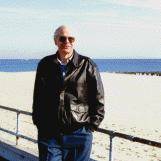
Ted Mooney, P.E.
Striving to live Aloha
(Ted can offer longterm or instant help)
finishing.com - Pine Beach, New Jersey
March 8, 2011
Q. I have a 6" diameter by 8' long galvanized steel stove pipe for a wood burning stove. I would like to copper plate it. How can I do that? What would you recommend - method, chemicals, efficient bath for long cylinder, etc.?
Thanks!
- Eastsound, Washington, USA
January 1, 2013
A. Hi Jay. First, I think you need to determine whether this will be a worthy finish if you succeed. Presumably it's for indoor use, as it will have no corrosion resistance. Second, it may not look too good, as you might not be able to successfully lacquer a hot stove pipe. So please try a small item before fooling with an 8 foot long one.
The galvanizing will be removed by the pretreatment process, and you will be doing the copper plating onto steel. If you don't want to send the stove pipe to a plating shop for copper plating, you can try a pen plating / brush plating outfit, available from a hobby plating supplier. There's a good chance you'll find it a humbling experience, so I'd urge you to try a small item, or practice on scrap, not potentially ruin an important item. Good luck.
Regards,
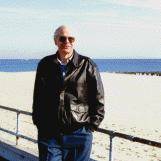
Ted Mooney, P.E.
Striving to live Aloha
(Ted can offer longterm or instant help)
finishing.com - Pine Beach, New Jersey
January 1, 2013
Q. I am soldering closed a bunch of little copper rings I've made from copper wire for some jewelry. I used Copper Soldering Paste (for plumbers I think), but the solder is actually a gray/silver color, so each little copper ring has a silver/gray spot where I soldered the seam.
What's the simplest way of copper plating the solder-spot using vinegar? Will the effect wear off over time?
- San Antonio Texas
February 9, 2013
A. Hi Canny. I liked Philip Camp's response about using copper powder mixed with thinned varnish.
Vinegar based plating is for students to learn a science lesson and is not intended, and won't work, for any practical application. Plating from copper sulphate on top of the copper powder and varnish will work better . . . but you're still talking about hobbyist plating which is mere millionths of an inch thick; it will wear off very quickly I'm afraid.
I'm no artist but the best approach may be to carefully mask the area, then apply the flux to only a tiny dot so there is no visible solder. With less precision, this is what plumbers do when they solder copper pipes, i.e., they are careful to only sand and flux as much as necessary for the joint, and let the un-sanded oxide serve as a mask. Good luck.
Regards,
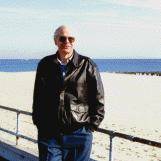
Ted Mooney, P.E.
Striving to live Aloha
(Ted can offer longterm or instant help)
finishing.com - Pine Beach, New Jersey
February 10, 2013
Q. Hi, I've renovating a lot of old apartments recently and end up with some old brass and copper bits and ends, currently I cut them up, toss them in a bucket and bring them down to a local scrap yard. I lose on the price of the copper because in a majority of cases there is a brass fitting attached to the copper pipe scraps, is there any process like the above method for separating the copper from the brass, as opposed to sweating off the individual parts which takes too much time.
Bernard AlainGeneral Trade - Ottawa, Ontario, Canada
February 18, 2013
Q, A, or Comment on THIS thread -or- Start a NEW Thread