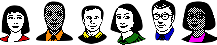
Metal finishing Q&As since 1989
-----
Layers of plating not fusing
January 7, 2018
Q. Hi
I'm using a home plating kit to plate brass musical instrument valves in copper then nickel to bring them back to size. It is useful to be able to put more than one layer of plating on to fill corroded areas, or to add material if the component is still undersize after one coating.
With both the copper and the nickel, I am finding that whereas there is a good bond between the plating and the brass, if I fit the component, prepare the piece as before and plate again, the second layer of plating does not bond to the first.
I am preparing the components in an ultrasonic bath with a Kemet cleaning solution that contains phosphoric acid. I then rinse in distilled water.
I have the electrolyte at around 23-27 °C and am using approx. 0.2 Amps per square inch of surface area. The electrolyte is quite new and I have had this problem since I started.
All help gratefully received.
Tom
Hobbyist/ commercial - Sheffield, Yorkshire, UK
A. Hi Tom. Actually, "failure to fuse" is not a strange phenomena but can be the normal expected condition if you don't take efforts to deal with it :-)
Just as the base metal must be properly cleaned and activated for the first layer of plating to stick to it, that first layer of plating must be active for the next layer to stick to it. Plating does not adhere in the fashion of glue adhering to the surface, but as a result of the plating molecularly bonding with the substrate. If the surface after the first layer of plating is not clean, the second layer of plating will not stick. If excessive brighteners were used in the first layer, the second layer will not stick, and if the first layer has been hanging around too long, building up an oxide film, the plating will not stick.
Please examine exactly what you are doing after the first layer of plating has been deposited, and before the second layer is added, and see if you are doing something like handling the parts, letting them get dirty, letting the plating "age", etc. One thing that may be necessary is a "nickel strike" -- a very thin layer of nickel plating deposited from a dilute and highly acidic special nickel solution to activate a layer deposited earlier and which has grown passive. Good luck.
Regards,
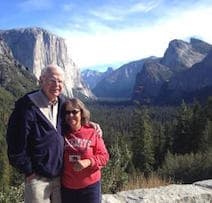
Ted Mooney, P.E. RET
Striving to live Aloha
finishing.com - Pine Beach, New Jersey
January 2018
Q. Thank you for this Ted. I appreciate that the deposition of metal happens at molecular level, and my previous advisor (the person who makes up the kits I use in the UK) has stressed the necessity of careful surface preparation, which I have been following as best I can.
The odd thing is that my surface preparation is the same for the subsequent layer of plating as for the first - ultrasonic bath with phosphoric acid solution. Given what you say, my conclusion must be that while that preparation is sufficient for brass, it is not sufficient to achieve deposition on either a copper or nickel plated surface. I have some HCL (masonry cleaner) that I can use - I will try that. Do you have any other suggestions?
Thanks again
Tom
Tom Fisher Horns - Derbyshire UK
January 9, 2018
A. Hi again, Tom. The most common procedure is to copper plate, rinse, and immediately nickel plate (without any re-cleaning or activating required) -- but this doesn't seem like it will suit your needs.
You seem to have two different situations to deal with:
1. an inactive copper layer to which you'd like to add nickel plating or more copper plating
2. an inactive nickel layer to which you'd like to add more nickel.
You'll find dozens of threads about situation 1 on this site because it is so frequently done for things like "show chrome" plating. But I've never heard of using phosphoric acid as an activator; HCl is probably a fine activator.
The second case, nickel on nickel, is going to require a Wood's Nickel Strike (which we also have many threads about) because nickel will get really inactive after delays and handling, and you're probably not going to be able to re-activate it with any simple acid dip.
Regards,
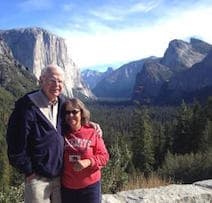
Ted Mooney, P.E. RET
Striving to live Aloha
finishing.com - Pine Beach, New Jersey
January 2018
Q, A, or Comment on THIS thread -or- Start a NEW Thread