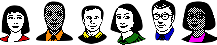
Metal finishing Q&As since 1989
-----
Zinc Plating fails 96-hour Salt Test
May 18, 2017
Q. I am struggling with getting my Zinc plated inserts to pass the 96-hour Salt Spray Test. The Zinc plating is 8 µm to 10 µm thick. The inserts have a clear trivalent Chromate coating, and the Chromate has a sealant as well.
The inserts pass the 96-hour SST coming from the plater. After over-molding the rubber the inserts exhibit white rust after as few as 24 hours in the test tank. The inserts we tested aren't bashed around after plating, so I doubt the plating is compromised enough by shipping to have them corrode so early.
Here is the process to mold the inserts.
1) acetone
[on
eBay or
Amazon (adv.)] to clean and prep the inserts for bonding agent.
2) Apply Chemlok 205, allow to set and then apply Chemlok 252.
3) Once these are dried the inserts are placed into the tool which is 320 °F
4) Mold dwell time is 700 seconds.
Would any of these operations above compromise the plating? I wonder about the Acetone but seriously doubt that is the root cause of the premature corrosion.
I've been struggling to be successful for almost a year now and still end up getting white rust as early as 24 hours. I don't know what else to try to get the parts to pass.
Help me Obi-Wan Kenobi ... You're my only hope.
Supply Chain Manager - Burnsville, Minnesota USA
Ed. note: Sorry, this RFQ is old & outdated, so contact info is no longer available. However, if you feel that something technical should be said in reply, please post it; no public commercial suggestions please ( huh? why?)
A. Hi Timothy. Acetone is generally considered non-destructive to chromate finishes, so I doubt that #1 is the problem. I doubt that solvents like in #2 are the problem either. Fresh chromate is only good for 140 °F, "cured" chromate for somewhat higher temperatures.
The first thing I'd do is make sure the parts are not molded until at least 24 hours after they are plated. If that has already been done, you're down to two possible paths:
a). Finding an alternate chromate vendor who promises higher temperature resistance (today's trivalent chromates were developed on an emergency basis as a substitute for hexavalent chromate, with attention paid to salt spray hours and little else, so they are highly proprietary and not all the same), or
b). Try to reduce the damage caused by the heat. I'd try some silicone sleeves on the parts during the baking process if possible, and see if that makes any difference, i.e., whether preventing atmospheric exposure while hot helps. If that doesn't work, is it possible to screw the exposed stud into any kind of heat sink so the chromate temperature stays lower?
Luck and Regards,
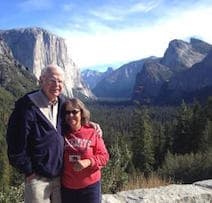
Ted Mooney, P.E. RET
Striving to live Aloha
finishing.com - Pine Beach, New Jersey
May 2017
A. Trying a silicated 'leachant-sealant' over your passivate would be worth a shot. Silicates are corrosion inhibitors, and in conjunction with hexavalent chromates or hex chrome engendering 'trivalent passivates' significantly improve the corrosion protection through synergistic action. Many suppliers handle such products under the names JS500, Superseal, Hyperseal, etc.

Tom Rochester
CTO - Jackson, Michigan, USA
Plating Systems & Technologies, Inc.


May 24, 2017
Q, A, or Comment on THIS thread -or- Start a NEW Thread